Molded shafts offer a streamlined and durable solution for connecting components, replacing traditional methods with greater precision and efficiency. This article provides Molded Shafts Explained, covering their manufacturing processes, applications, advantages, and how to select the right one for your needs. We’ll delve into different materials, design considerations, and the future of this innovative technology.
⚠️ Still Using Pen & Paper (or a Chalkboard)?! ⚠️
Step into the future! The Dart Counter App handles all the scoring, suggests checkouts, and tracks your stats automatically. It's easier than you think!
Try the Smart Dart Counter App FREE!Ready for an upgrade? Click above!
Molded Shafts Explained: An In-Depth Look
Molded shafts explained necessitates understanding that they are essentially components created through molding processes, typically involving injecting molten material into a mold cavity to produce a desired shape. This contrasts with machining or other subtractive manufacturing techniques. The result is a part with high dimensional accuracy and consistency, often used in applications requiring precise rotational movement or power transmission.
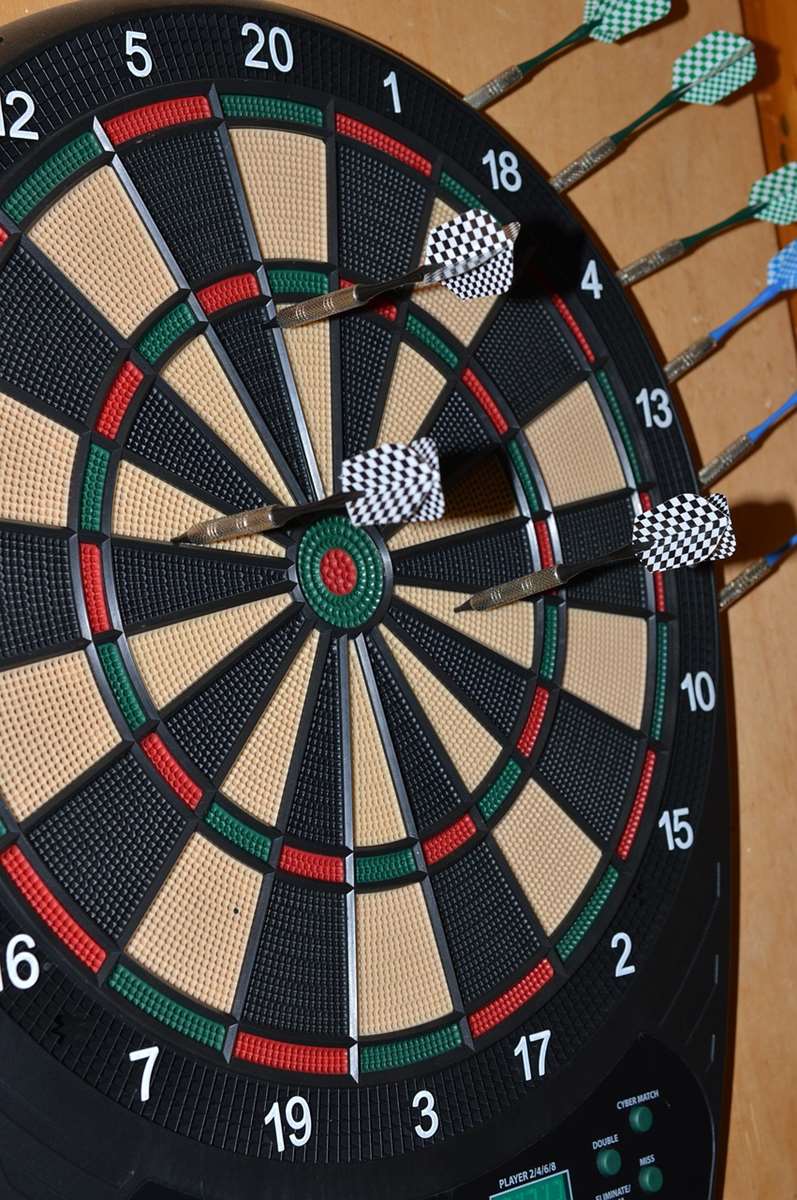
The Molding Process: A Closer Examination
The molding process is crucial to the quality and performance of molded shafts. It usually involves these key steps:
- Mold Design: The mold must be designed with precision to ensure the final product meets the required specifications. This includes considerations for material shrinkage, venting, and cooling.
- Material Selection: The choice of material depends on the application’s requirements, such as load capacity, temperature resistance, and chemical compatibility. Common materials include various plastics and composite materials.
- Injection Molding: Molten material is injected into the mold cavity under high pressure. Precise control of temperature and pressure is essential to prevent defects like voids or warping.
- Cooling and Solidification: The material is allowed to cool and solidify within the mold. Cooling channels are often integrated into the mold to accelerate this process.
- Ejection: Once the material has solidified, the mold is opened, and the finished shaft is ejected.
- Finishing (Optional): Some molded shafts may require additional finishing steps, such as trimming, surface treatment, or machining, to meet specific requirements.
Benefits of Using Molded Shafts
Compared to traditional methods of manufacturing shafts, such as machining, molded shafts offer several advantages:
- Cost-Effectiveness: Molding is typically more cost-effective for high-volume production runs than machining. The initial investment in the mold can be significant, but the per-part cost is usually lower.
- Design Flexibility: Molding allows for complex geometries and intricate features that may be difficult or impossible to achieve with machining.
- Material Versatility: A wide range of materials can be used in the molding process, allowing for optimization based on the specific application requirements.
- High Precision and Consistency: Molding provides excellent dimensional accuracy and consistency from part to part, which is crucial for applications requiring precise performance.
- Reduced Material Waste: Molding generates less material waste compared to subtractive manufacturing processes like machining.
- Integration of Features: Features like gears, splines, and bearings can be integrated directly into the molded shaft during the molding process, reducing the need for secondary operations.
These benefits make molded shafts an attractive option for a wide range of applications.
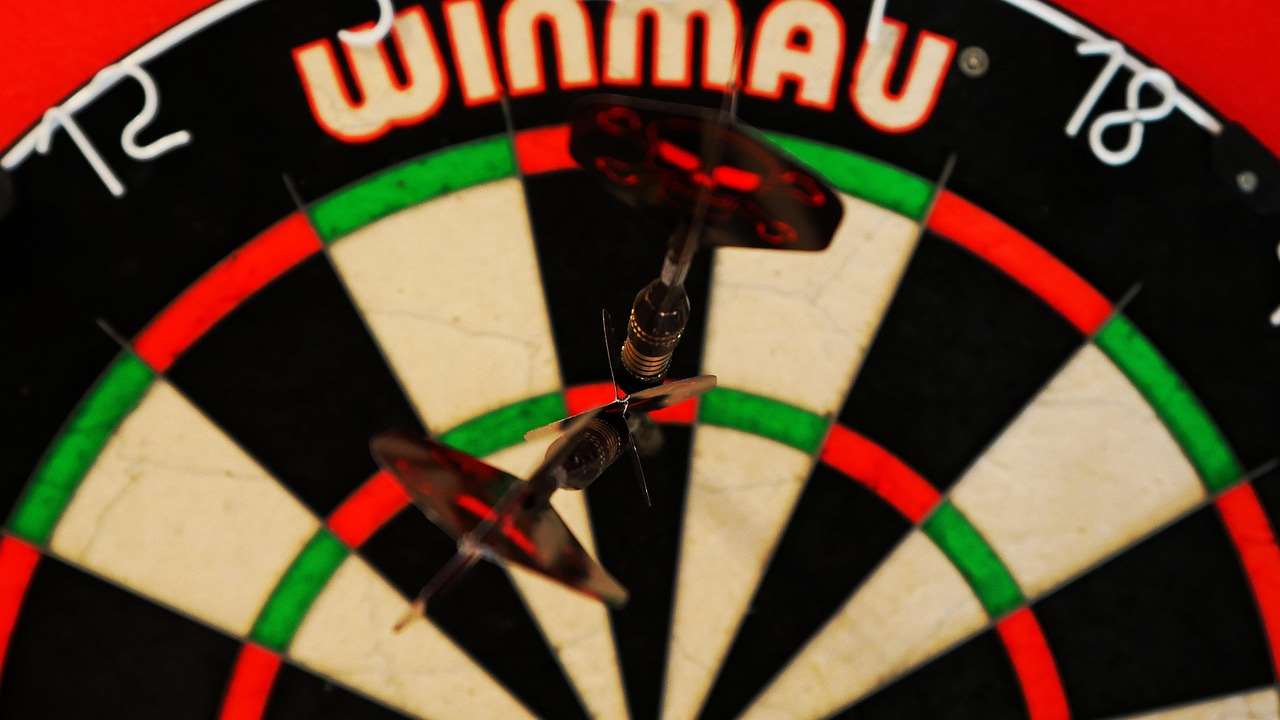
Common Materials Used in Molded Shafts
The selection of materials for molded shafts depends heavily on the intended application. Here are some commonly used materials:
- Plastics:
- Acrylonitrile Butadiene Styrene (ABS): Known for its impact resistance and durability.
- Polycarbonate (PC): Offers high strength and temperature resistance.
- Nylon (Polyamide (PA)): Provides excellent wear resistance and low friction.
- Polyoxymethylene (POM) (Acetal): Known for its stiffness, low friction, and dimensional stability.
- Composite Materials:
- Fiber-Reinforced Plastics (FRP): Combine the strength of fibers (e.g., glass or carbon) with the flexibility of plastics.
Each material has its unique properties, making it suitable for different applications. For example, a molded shaft used in a high-temperature environment might require a material like Polycarbonate, while one used in a high-wear application might benefit from Nylon.
Applications of Molded Shafts
Molded shafts find use in a diverse array of industries due to their versatility and cost-effectiveness. These applications include:
- Automotive: Components in power steering systems, window regulators, and seat adjustment mechanisms.
- Consumer Electronics: Drive shafts in printers, scanners, and other office equipment.
- Medical Devices: Actuators in medical pumps and diagnostic equipment.
- Industrial Machinery: Components in pumps, motors, and gearboxes.
- Aerospace: Control linkages and actuators in aircraft systems.
- Sporting Goods: Drive systems in some recreational equipment. Consider how molded shafts can benefit even choosing best dart equipment by providing improved balance and durability.
The increasing demand for lighter, more efficient, and cost-effective components is driving the adoption of molded shafts in these and other industries.

Design Considerations for Molded Shafts
Designing effective molded shafts requires careful consideration of several factors:
- Load Capacity: The shaft must be able to withstand the applied loads without deforming or failing.
- Dimensional Accuracy: Precise dimensions are essential for proper fit and function.
- Surface Finish: The surface finish must be appropriate for the application to minimize friction and wear.
- Environmental Conditions: The shaft must be able to withstand the operating environment, including temperature, humidity, and chemical exposure.
- Material Selection: As previously mentioned, the material must be chosen to meet the specific requirements of the application.
- Molding Process: The design must be compatible with the chosen molding process to ensure manufacturability.
Proper design can optimize the performance and lifespan of molded shafts.
Critical Design Elements
Several specific design elements require careful attention when designing molded shafts:
- Wall Thickness: Consistent wall thickness is essential to prevent warping and ensure uniform cooling.
- Ribs and Gussets: These features can be used to increase the stiffness and strength of the shaft without adding excessive weight.
- Draft Angles: Draft angles are necessary to facilitate ejection of the shaft from the mold.
- Undercuts: Undercuts can be challenging to mold and may require special mold designs or secondary operations.
- Gate Location: The location of the gate (where the molten material enters the mold) can affect the flow of material and the properties of the finished part.
Quality Control and Testing
Rigorous quality control and testing are essential to ensure that molded shafts meet the required specifications. Common testing methods include:
- Dimensional Measurement: Using coordinate measuring machines (CMMs) or other precision instruments to verify dimensions.
- Visual Inspection: Checking for surface defects, such as scratches, voids, or warping.
- Mechanical Testing: Evaluating the strength and stiffness of the shaft under load.
- Material Testing: Verifying the properties of the material, such as tensile strength and elongation.
- Non-Destructive Testing (NDT): Using techniques like ultrasonic testing or radiography to detect internal defects.
Thorough testing helps ensure the reliability and performance of molded shafts in their intended applications.
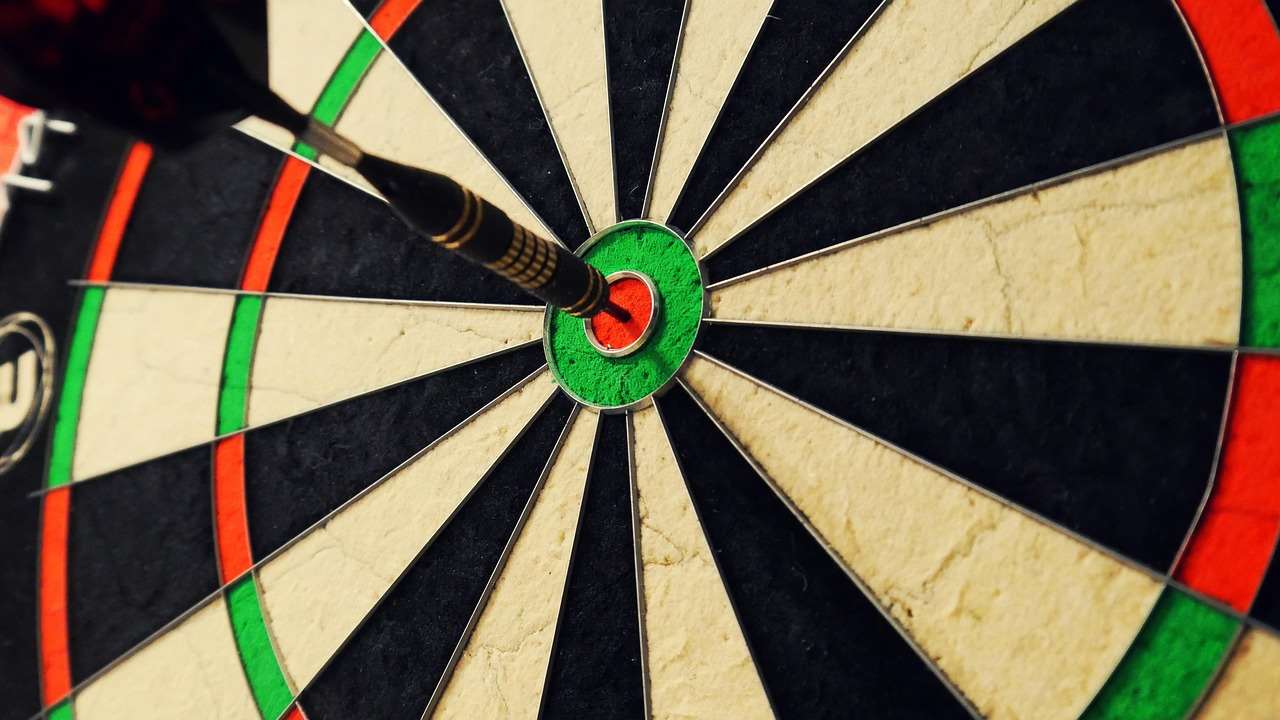
The Future of Molded Shafts
The future of molded shafts looks promising, with ongoing developments in materials, processes, and applications. Some key trends include:
- Advanced Materials: Development of new materials with improved strength, temperature resistance, and other properties.
- Process Optimization: Refinement of molding processes to improve efficiency, reduce costs, and enhance part quality.
- Additive Manufacturing: Integration of additive manufacturing (3D printing) techniques to create complex geometries and customized shafts.
- Smart Shafts: Embedding sensors and electronics into molded shafts to monitor performance and provide feedback.
These advancements will further expand the applications of molded shafts and enhance their performance in existing applications.
Selecting the Right Molded Shaft
Choosing the correct molded shaft involves considering the application’s specific demands:
- Determine Load Requirements: Understand the loads the shaft will encounter.
- Analyze Environmental Factors: Consider temperature, humidity, and chemical exposure.
- Define Dimensional Tolerances: Specify required precision.
- Choose the Appropriate Material: Select a material that meets performance criteria.
- Evaluate Cost-Effectiveness: Balance performance with budget considerations.
Consulting with a knowledgeable manufacturer can also help ensure you select the optimal shaft for your specific needs.
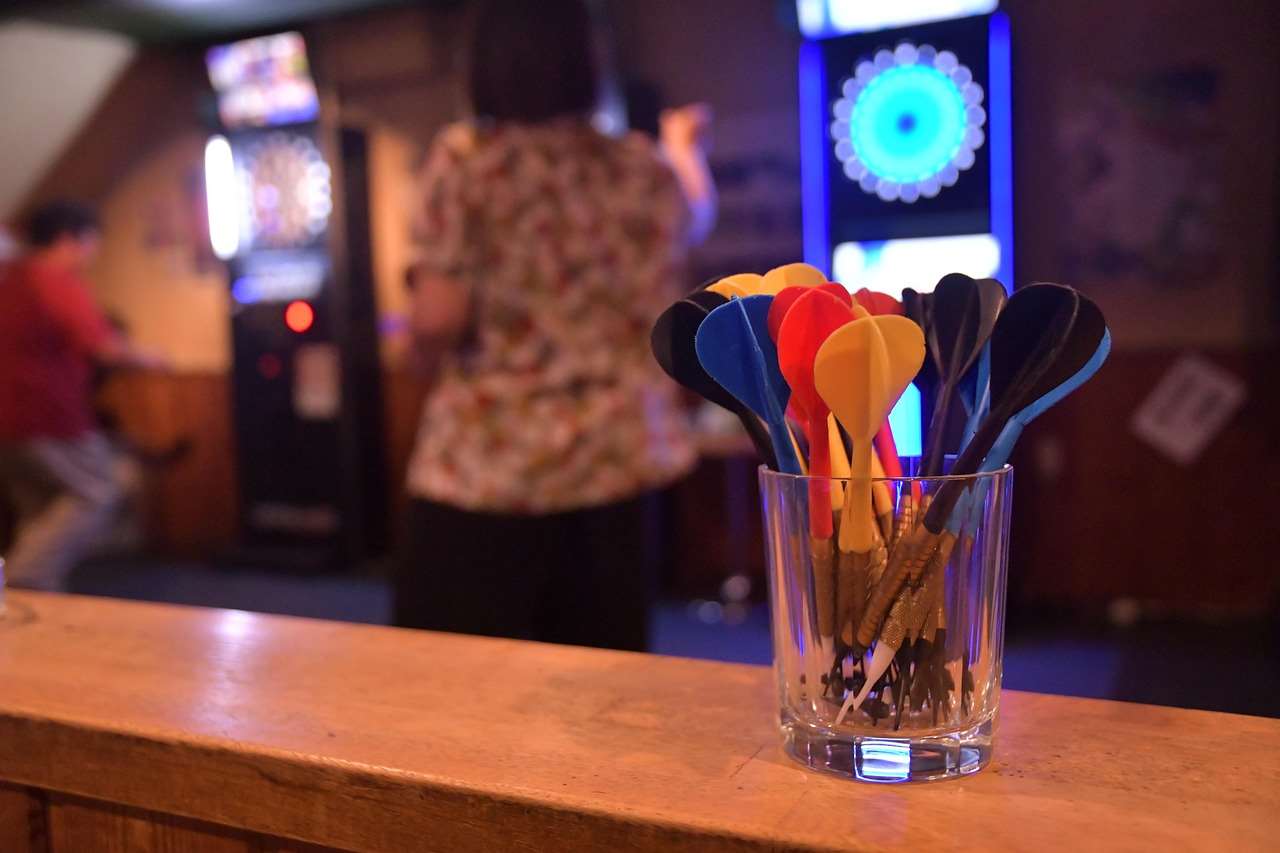
Conclusion
In conclusion, molded shafts explained demonstrate a versatile and efficient solution for a wide range of engineering applications. Their advantages in terms of cost-effectiveness, design flexibility, and material versatility make them an attractive alternative to traditional manufacturing methods. By understanding the molding process, material options, design considerations, and quality control measures, engineers can effectively utilize molded shafts to enhance the performance and reliability of their products. If you’re considering incorporating molded shafts into your next project, consider researching suppliers or seeking expert advice. Furthermore, if you’re interested in improving your dart game, understanding optimal lighting is crucial; explore our guide on Optimal Dartboard Lighting Solutions Guide to learn more.
Hi, I’m Dieter, and I created Dartcounter (Dartcounterapp.com). My motivation wasn’t being a darts expert – quite the opposite! When I first started playing, I loved the game but found keeping accurate scores and tracking stats difficult and distracting.
I figured I couldn’t be the only one struggling with this. So, I decided to build a solution: an easy-to-use application that everyone, no matter their experience level, could use to manage scoring effortlessly.
My goal for Dartcounter was simple: let the app handle the numbers – the scoring, the averages, the stats, even checkout suggestions – so players could focus purely on their throw and enjoying the game. It began as a way to solve my own beginner’s problem, and I’m thrilled it has grown into a helpful tool for the wider darts community.