The best lubricant for movable points depends heavily on the application, but for many common uses, a high-quality silicone-based lubricant is the top choice. This article will delve into the specifics of choosing the best lubricant for movable points, considering various materials and applications, and provide guidance on proper application and maintenance.
⚠️ Still Using Pen & Paper (or a Chalkboard)?! ⚠️
Step into the future! The Dart Counter App handles all the scoring, suggests checkouts, and tracks your stats automatically. It's easier than you think!
Try the Smart Dart Counter App FREE!Ready for an upgrade? Click above!
Selecting the right lubricant can significantly impact the longevity and performance of your equipment. A poorly chosen lubricant can lead to increased friction, wear, and even damage. Therefore, understanding the factors that influence lubricant selection is crucial for maintaining your equipment and ensuring smooth operation. This guide covers various factors to consider, such as the type of material involved, the operating environment, and the desired level of lubrication.
Choosing the Best Lubricant for Movable Points: A Comprehensive Guide
Finding the best lubricant for movable points isn’t just about picking something oily; it’s about understanding the specific needs of your application. Different materials require different types of lubricants to avoid damage and ensure optimal performance. Factors like temperature, load, and speed also play crucial roles. Let’s break down the key considerations:
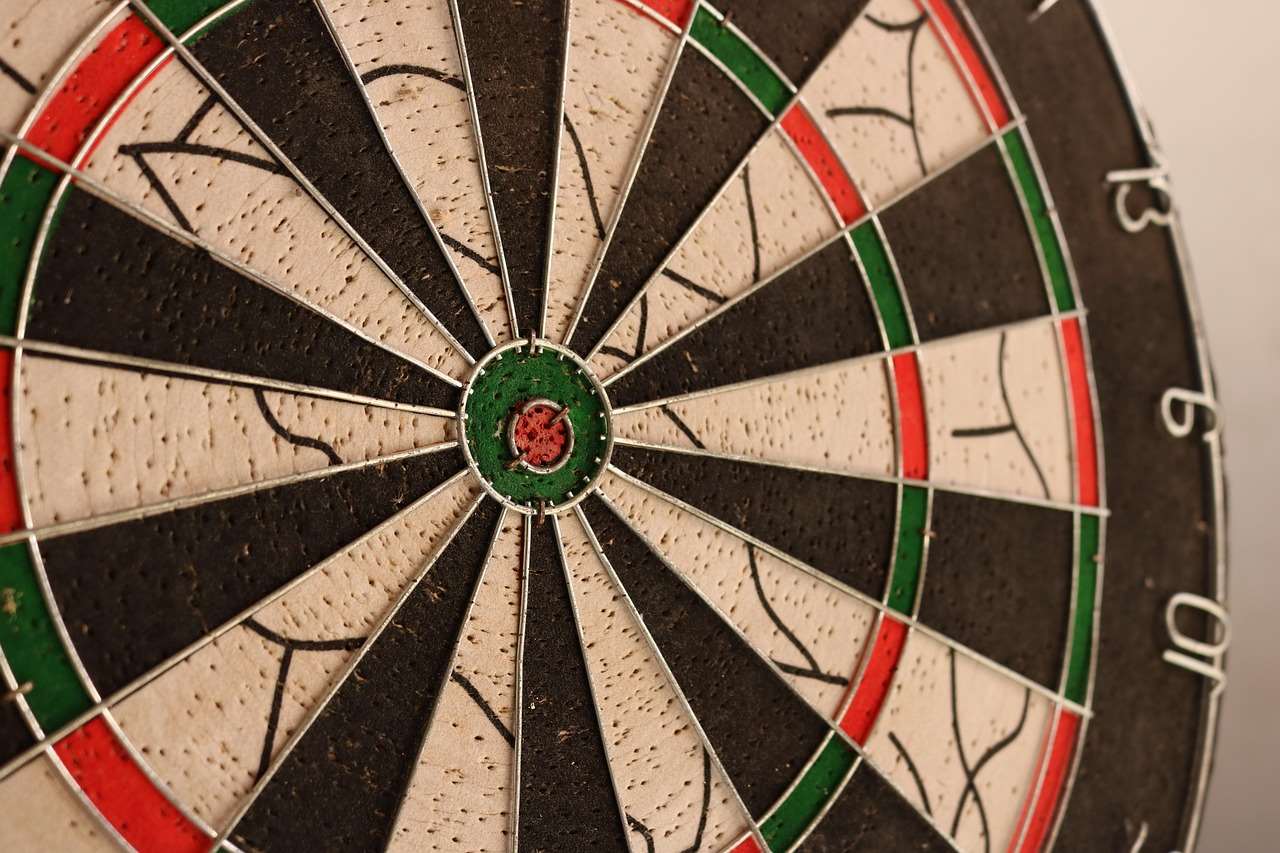
Material Compatibility
The first and arguably most important factor is material compatibility. Using the wrong lubricant on a specific material can lead to corrosion, swelling, or degradation. For example, rubber and plastic components might be damaged by oil-based lubricants, while metal components might require a lubricant that prevents rust and corrosion. Always consult the manufacturer’s specifications for your specific equipment to ensure compatibility. Some common materials and suitable lubricants include:
- Metals (Steel, Aluminum, Brass): Silicone-based lubricants, white lithium grease, or specialized metal-to-metal lubricants.
- Plastics (Nylon, Teflon): Silicone-based lubricants or specialized plastic-compatible lubricants. Avoid oil-based lubricants.
- Rubber: Silicone-based lubricants are generally safe for rubber, but always test on a small, inconspicuous area first.
Remember that even within these categories, variations in specific formulations can affect compatibility. Always refer to the manufacturer’s instructions for both your equipment and the lubricant.
Operating Environment
The operating environment significantly impacts lubricant choice. High-temperature applications necessitate lubricants with high temperature resistance, while low-temperature applications may require lubricants that remain fluid at freezing temperatures. Consider these factors:
- Temperature Range: The lubricant must be able to perform effectively within the expected temperature range. Extreme temperatures can cause lubricants to thicken or thin, reducing their effectiveness.
- Moisture Exposure: If your movable points are exposed to moisture, a water-resistant or water-displacing lubricant is crucial to prevent corrosion.
- Dust and Dirt: Environments with high dust and dirt levels may necessitate lubricants that resist contamination and maintain their lubricating properties.
Understanding your equipment’s operating conditions is paramount in making an informed decision about the best lubricant for movable points.
Types of Lubricants
Many types of lubricants are available, each with its own strengths and weaknesses. The ideal choice depends on your specific needs. Here are some common options:
- Silicone-Based Lubricants: A versatile and widely used option, suitable for many materials and operating environments. They are generally inert, resistant to water, and have a wide temperature range. This makes them a great all-around choice for many applications, often the best lubricant for movable points in everyday use.
- Oil-Based Lubricants: Effective for metal-on-metal applications, but can be less suitable for plastics and rubbers. They may also attract dust and dirt.
- Grease-Based Lubricants: Offer thicker, longer-lasting lubrication, ideal for applications with high loads or slow speeds. They are less susceptible to being wiped off.
- Dry Lubricants (Teflon, Graphite): Suitable for applications requiring minimal lubrication, often used where oil or grease is undesirable. However, they may not offer the same level of protection as liquid lubricants.
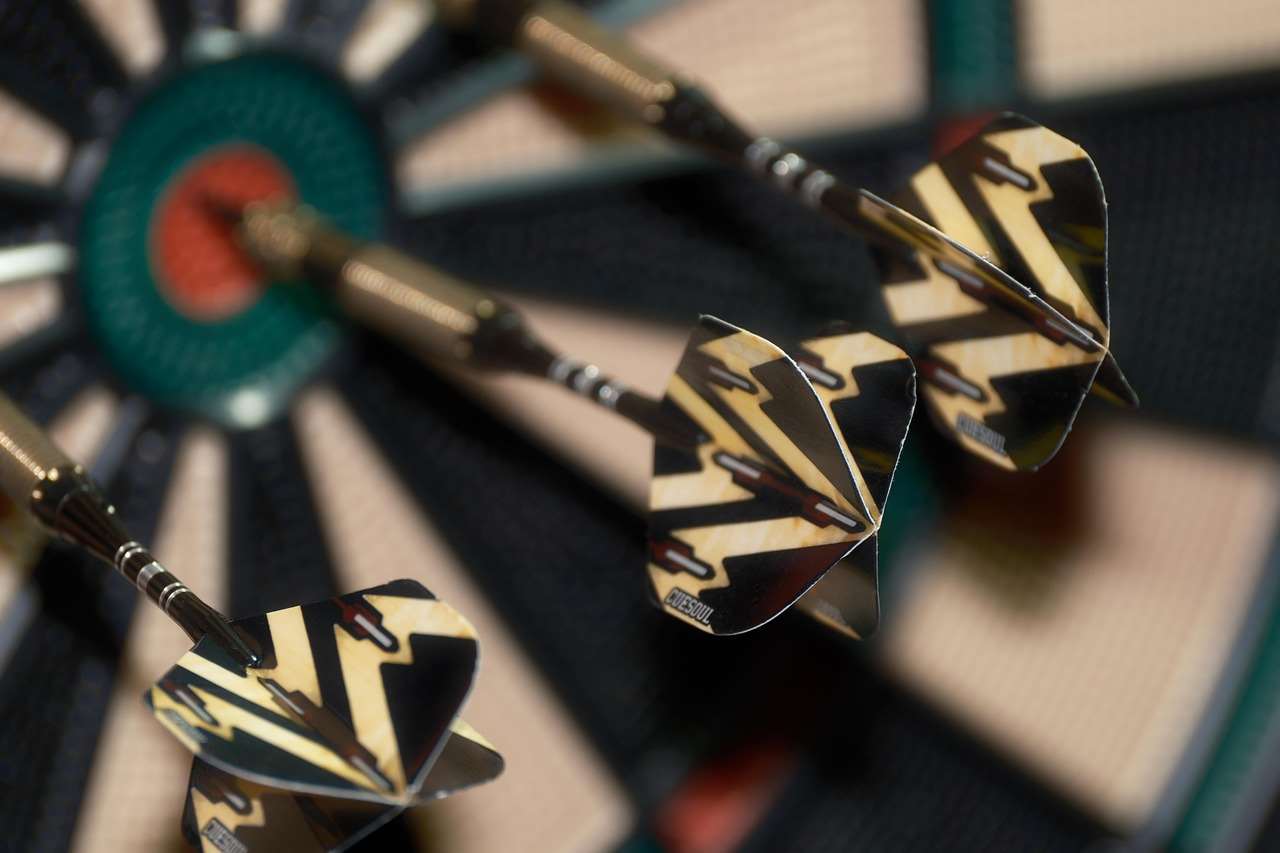
Application and Maintenance
Proper application and regular maintenance are vital for maximizing the lifespan and effectiveness of your lubricant. Avoid over-lubrication, as this can attract dust and dirt, leading to increased friction. Apply a small amount to the movable points, and wipe off any excess.
Regular inspection and re-lubrication are essential. How often you need to reapply lubricant depends on the operating conditions and the type of lubricant used. Always consult the manufacturer’s recommendations for specific maintenance schedules. Cleaning the movable points before re-lubrication can remove accumulated dust, dirt, and old lubricant, ensuring optimal performance.
Specific Applications and Lubricant Recommendations
While silicone-based lubricants are often a good starting point, some applications might require more specialized lubricants. Here are a few examples:
- Precision Instruments: For applications requiring extremely precise movement, specialized high-purity lubricants may be necessary.
- High-Temperature Applications: In high-temperature environments, high-temperature greases or specialized lubricants with appropriate temperature ratings are essential.
- Food Processing Equipment: Lubricants that meet food-grade standards are necessary to prevent contamination.
Choosing the right lubricant can be crucial for the proper function of your equipment. Selecting the best lubricant for movable points requires consideration of material compatibility, the operating environment, and the specific application.

Troubleshooting Common Issues
Even with the right lubricant, you might encounter issues with your movable points. Here are some common problems and solutions:
- Excessive Friction: This could be due to insufficient lubrication, incorrect lubricant type, or contamination. Check your lubricant level, consider using a more suitable lubricant, or clean the movable points thoroughly.
- Sticking or Binding: This may indicate incorrect lubricant type, contamination, or wear and tear. Try a different lubricant or consider replacing the components.
- Corrosion: This often results from moisture or incompatible lubricants. Make sure to use a water-resistant lubricant and consider anti-corrosion treatments if necessary. Remember, using the correct best lubricant for movable points helps prevent this.
Regular maintenance and proper lubrication significantly extend the lifespan of your equipment and minimize the risk of these problems.
Maintaining your equipment properly is vital to its longevity and efficiency. For more insights into maintaining your equipment, check out our guide on Darts Equipment Maintenance Customization. This comprehensive guide dives deep into extending the life of various components.
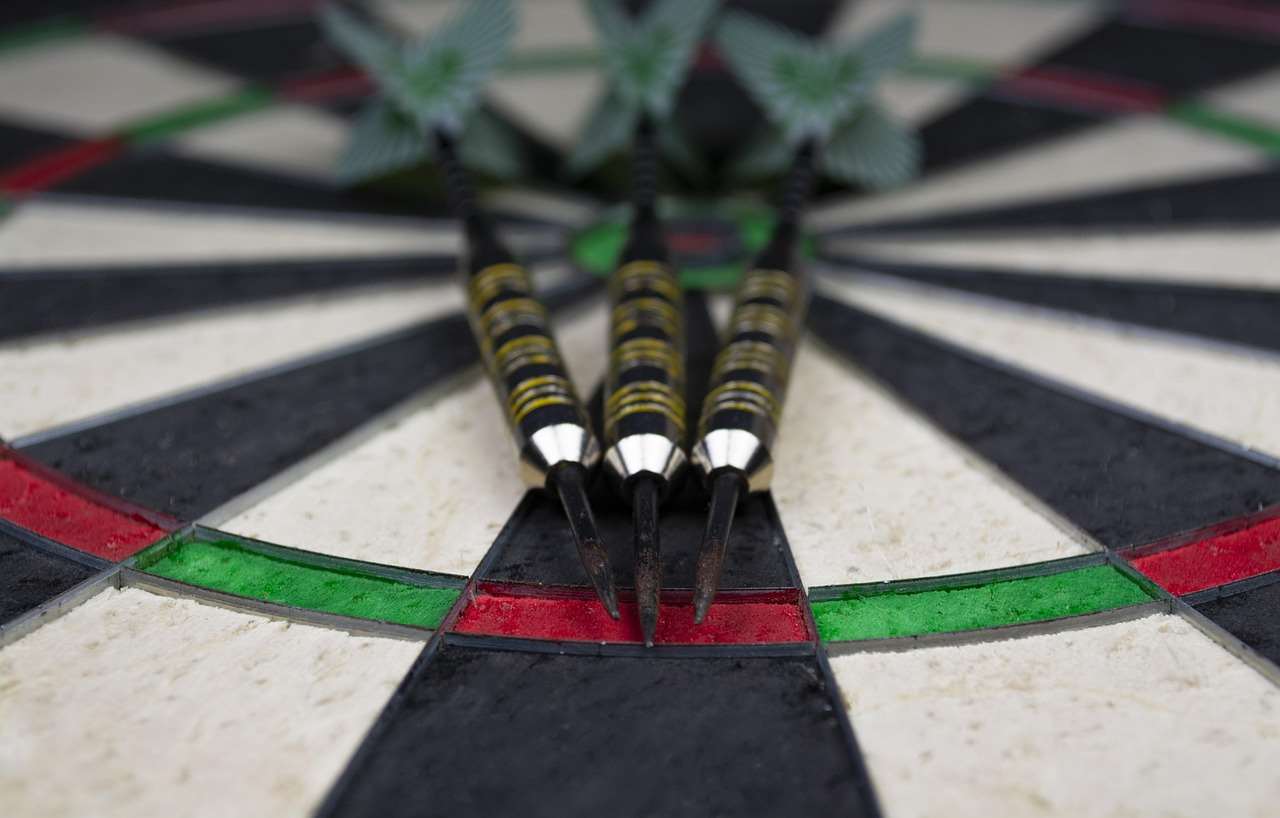
Beyond the Basics: Advanced Considerations
For more demanding applications, you might need to consider more advanced factors when choosing the best lubricant for movable points. These include:
- Viscosity: The viscosity (thickness) of the lubricant influences its flow and lubrication properties. Higher viscosity lubricants are better for high loads, while lower viscosity lubricants are suitable for high speeds.
- Additives: Lubricants often contain additives to enhance their performance. These might include anti-wear additives, extreme-pressure additives, or corrosion inhibitors.
- Food Safety: In food-processing applications, lubricants must meet strict food-grade standards to prevent contamination.
For extremely specialized needs, consulting a lubrication specialist can provide expert advice and ensure optimal performance and longevity.
If you’re interested in creating a customized setup for your equipment, you might find our guide on Custom dartboard cabinet useful. It details various customization options.
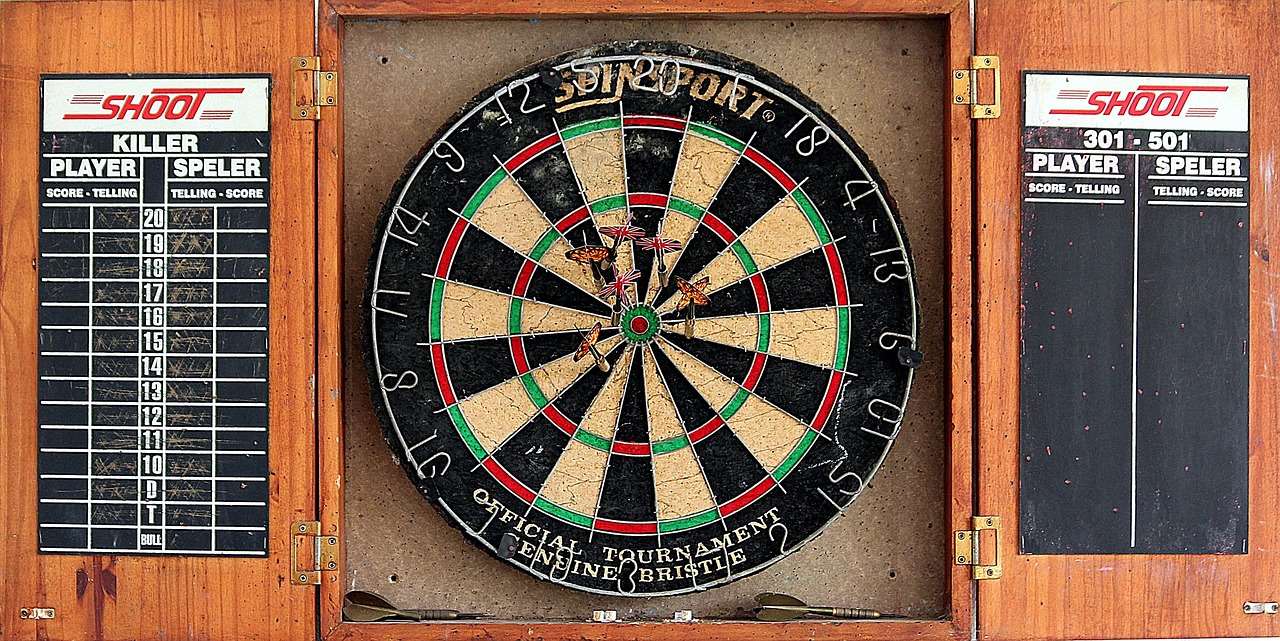
Conclusion
Selecting the best lubricant for movable points is a critical aspect of maintaining equipment and ensuring optimal performance. By considering material compatibility, operating environment, and the type of lubricant, you can significantly extend the life of your equipment and prevent costly repairs. Remember to always consult the manufacturer’s recommendations for both your equipment and the lubricant you choose. Regular maintenance and proper lubrication practices are key to keeping things running smoothly and efficiently. Don’t forget to check out our guide on Maintaining movable dart points for more specific tips and advice!
Ready to optimize your equipment’s performance? Start exploring the best lubricants for your needs today!
Hi, I’m Dieter, and I created Dartcounter (Dartcounterapp.com). My motivation wasn’t being a darts expert – quite the opposite! When I first started playing, I loved the game but found keeping accurate scores and tracking stats difficult and distracting.
I figured I couldn’t be the only one struggling with this. So, I decided to build a solution: an easy-to-use application that everyone, no matter their experience level, could use to manage scoring effortlessly.
My goal for Dartcounter was simple: let the app handle the numbers – the scoring, the averages, the stats, even checkout suggestions – so players could focus purely on their throw and enjoying the game. It began as a way to solve my own beginner’s problem, and I’m thrilled it has grown into a helpful tool for the wider darts community.