Begrip point wear measurement is crucial for maintaining optimal performance and extending the lifespan of various tools and equipment, from dart points to industrial machinery components. This article will delve into the methods, importance, and best practices for measuring and addressing point wear, ensuring accuracy and efficiency in your applications. We’ll explore different techniques, technologies, and preventative measures to help you make informed decisions about maintenance and replacement.
⚠️ Still Using Pen & Paper (Of een schoolbord)?! ⚠️
Stap in de toekomst! De Dart Teller -app behandelt alle scoren, stelt kassa voor, en volgt uw statistieken automatisch. It's easier than you think!
Probeer de Smart Dart Teller -app gratis!Klaar voor een upgrade? Klik hierboven!
Understanding Point Wear Measurement
Point wear measurement is the process of assessing the amount of material loss or degradation at the tip, edge, or point of a tool, component, or instrument. This measurement is vital because wear directly impacts performance, nauwkeurigheid, and overall lifespan. Ignoring point wear can lead to decreased efficiency, increased error rates, en uiteindelijk, premature failure.
Different types of wear can occur, inbegrepen:
- Abrasive wear: Caused by hard particles rubbing against a surface.
- Adhesive wear: Occurs when materials transfer between surfaces due to strong adhesion.
- Erosion: Wear due to the impact of particles carried by a fluid or gas.
- Corrosion: Degradation due to chemical reactions.
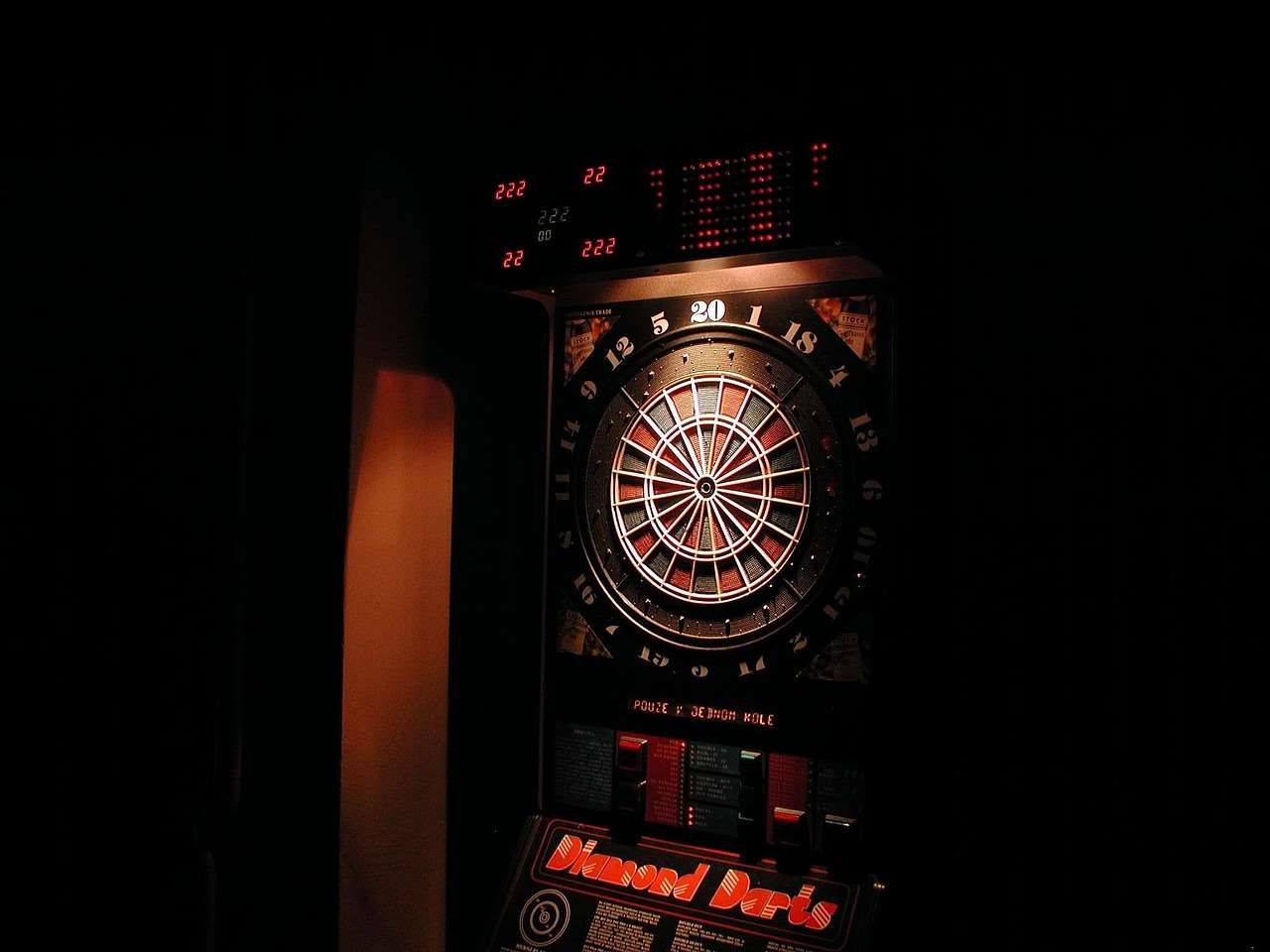
Why is Point Wear Measurement Important?
The significance of point wear measurement extends across numerous industries and applications. Consider these benefits:
- Improved Performance: Accurate measurement allows for timely maintenance, ensuring optimal performance.
- Reduced Downtime: Identifying wear early prevents unexpected failures and costly downtime.
- Extended Lifespan: Implementing preventative measures based on wear measurements prolongs the life of tools and equipment.
- Enhanced Safety: Monitoring wear in critical components enhances safety by preventing failures that could lead to accidents.
- Cost Savings: Proactive maintenance reduces the need for expensive repairs or replacements.
Bijvoorbeeld, in the context of dart playing, worn dart points can significantly affect the accuracy and consistency of throws. Regular assessment and maintenance, or replacement, can help improve scores and prevent damage to the dartboard. You can Kies de beste Dart -apparatuur.
Methods for Point Wear Measurement
Several methods exist for point wear measurement, each with its advantages and limitations. The choice of method depends on the application, the type of material, and the desired level of accuracy. Here are some common techniques:
Visual Inspection
Visual inspection is the simplest method, involving a close examination of the point’s condition with the naked eye or a magnifying glass. This method is subjective and primarily useful for detecting gross wear or damage. While limited in precision, it can provide a quick initial assessment.
Mechanical Measurement
Mechanical measurement involves using instruments like calipers, micrometers, or profilometers to measure the dimensions of the point. These tools provide more accurate quantitative data compared to visual inspection.
- Calipers and Micrometers: Suitable for measuring overall dimensions and changes in shape.
- Profilometers: Measure surface roughness and wear depth with high precision.
Optical Measurement
Optical measurement techniques use light to capture images or data about the point’s surface. These methods are non-contact and can provide detailed information without damaging the component.
- Microscopy: Provides magnified images of the surface, revealing wear patterns and defects.
- Laser Scanning: Creates a 3D model of the surface, allowing for precise measurement of wear volume and depth.
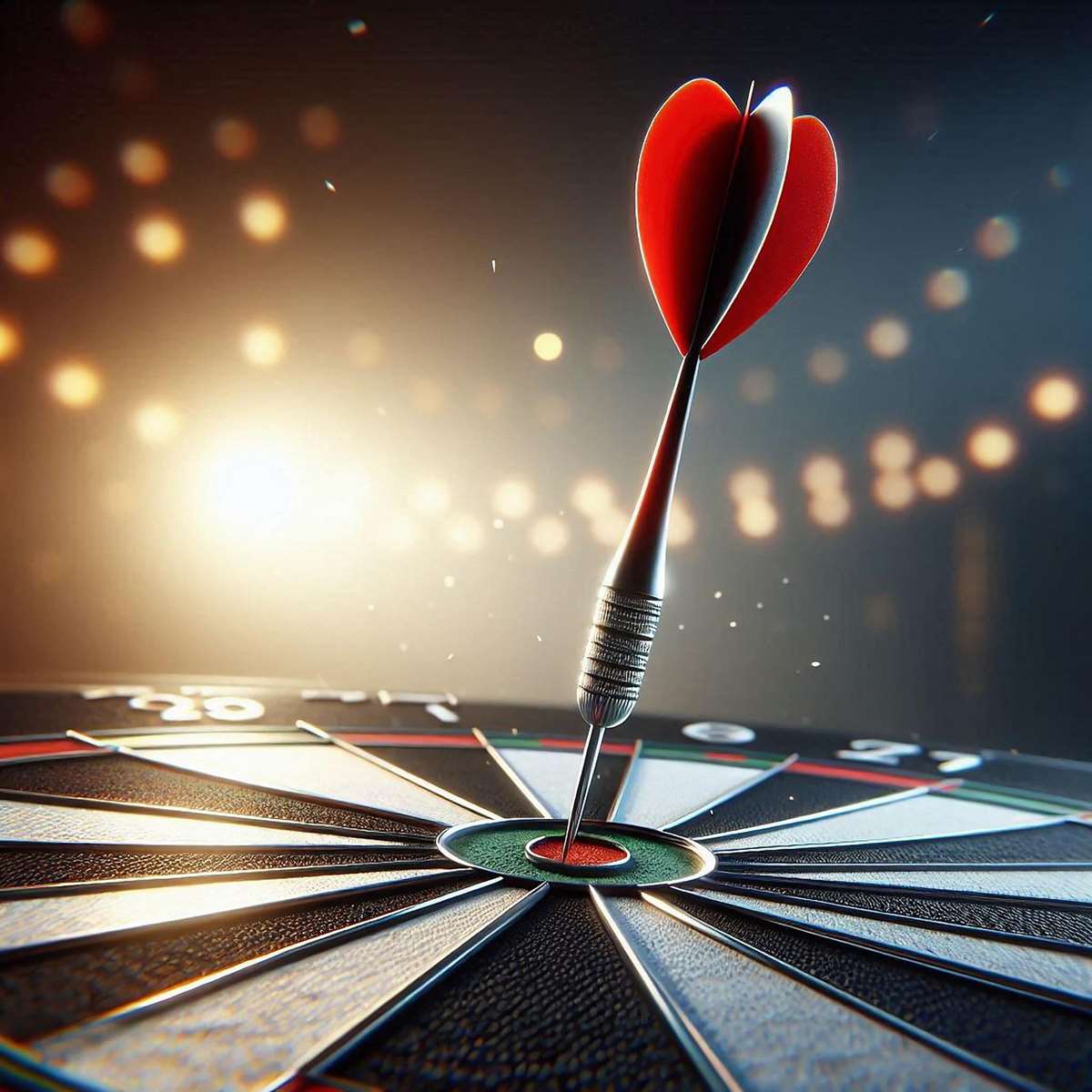
Weight Measurement
In some cases, measuring the weight loss of a component can provide an indication of wear. This method is suitable for applications where wear results in a significant reduction in material.
Important Note: This method assumes that all weight loss is due to wear and does not account for other factors like corrosion or contamination.
Non-Destructive Testing (NDT)
NDT methods can be used to detect wear and damage without compromising the integrity of the component. Common NDT techniques include:
- Ultrasonic Testing: Uses sound waves to detect internal flaws and measure material thickness.
- Eddy Current Testing: Detects surface and subsurface defects by inducing eddy currents in the material.
- Radiography: Uses X-rays or gamma rays to visualize internal structures and detect wear or damage.
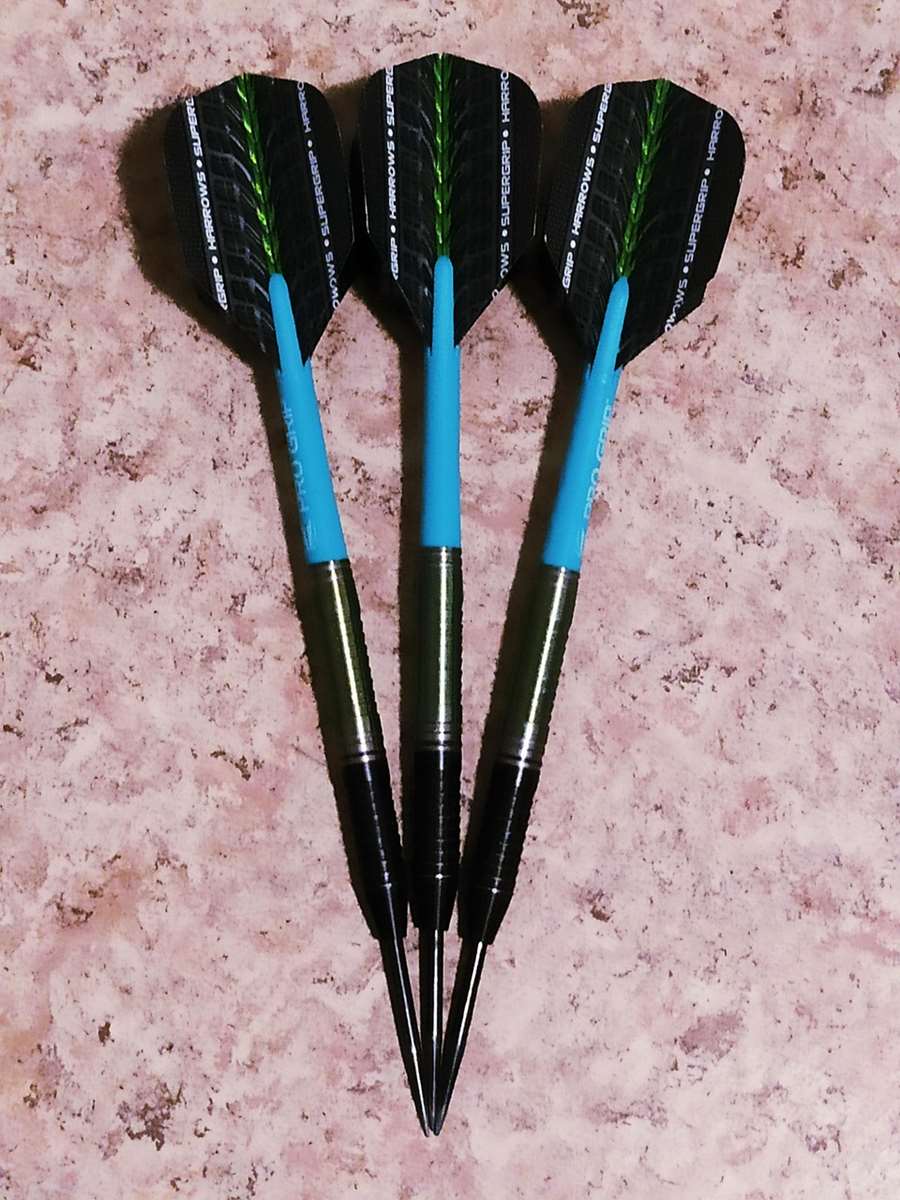
Factors Affecting Point Wear
Several factors can influence the rate and type of point wear. Understanding these factors is crucial for implementing effective preventative measures.
- Material Properties: The hardness, toughness, and corrosion resistance of the material play a significant role.
- Operating Conditions: Factors like temperature, pressure, and speed can accelerate wear.
- Lubrication: Proper lubrication reduces friction and wear between surfaces.
- Environmental Factors: Exposure to corrosive substances, abrasive particles, or extreme temperatures can accelerate wear.
- Load: The amount of force applied to the point affects the wear rate; higher loads typically cause faster wear.
Bijvoorbeeld, dart points made of softer metals will wear down faster than those made of harder materials like tungsten. Similarly, using a dartboard made of sisal fibers will extend the life of your dart points compared to using an electronic dartboard.
Preventative Measures for Reducing Point Wear
Implementing preventative measures can significantly reduce point wear and extend the lifespan of tools and equipment. Here are some effective strategies:
Proper Lubrication
Applying lubricants reduces friction and wear between moving parts. Choose a lubricant that is appropriate for the application and operating conditions.
Material Selection
Selecting materials with high wear resistance is crucial for applications where wear is a significant concern. Consider factors like hardness, toughness, and corrosion resistance.
Surface Treatments
Applying surface treatments like coatings or hardening processes can improve the wear resistance of components. Common surface treatments include:
- Hard Chrome Plating: Provides a hard, wear-resistant surface.
- Nitriding: Increases surface hardness and wear resistance by diffusing nitrogen into the material.
- Coatings: Applying specialized coatings can protect the surface from wear and corrosion.
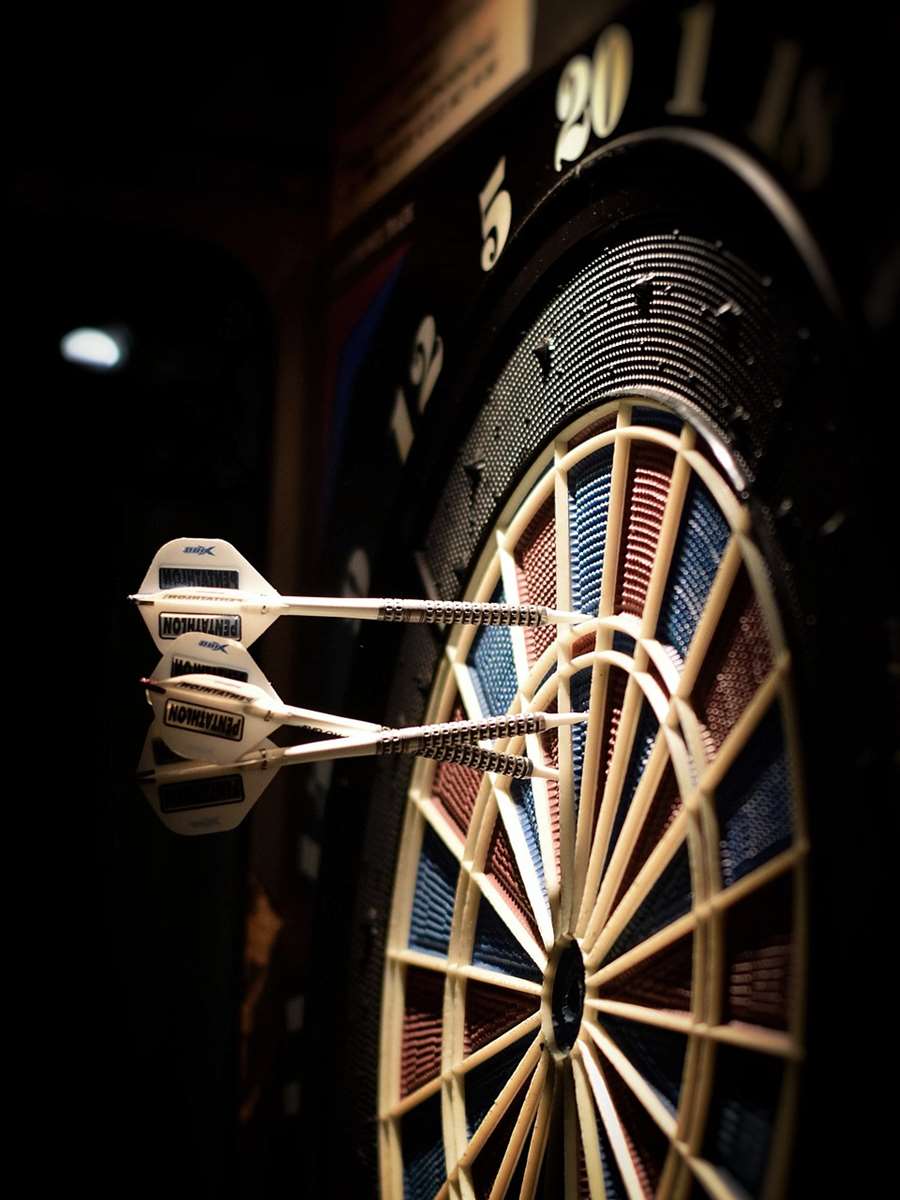
Regular Maintenance and Inspection
Implementing a regular maintenance and inspection schedule allows for the early detection of wear and damage. Address any issues promptly to prevent further degradation.
Optimizing Operating Conditions
Adjusting operating conditions to reduce stress and friction can minimize wear. This may involve reducing speed, load, or temperature.
Filtration
Using filters to remove abrasive particles from fluids or gases can reduce erosion and abrasive wear. This is particularly important in hydraulic systems and engines.
You might also consider Types Optimal Dartboard Lighting to better visually inspect your equipment.
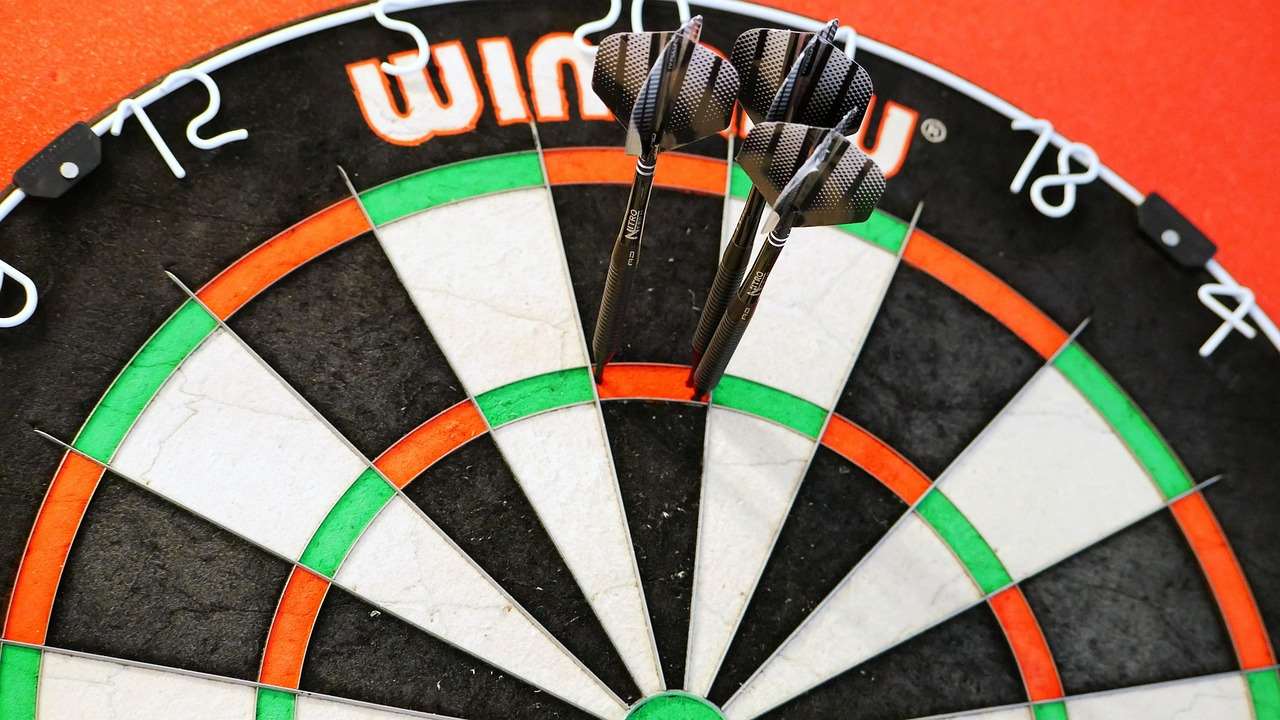
Case Studies and Examples
To illustrate the importance of point wear measurement, consider the following examples:
Manufacturing Industry
In machining operations, worn cutting tools can lead to inaccurate cuts, poor surface finishes, and increased scrap rates. Regular point wear measurement allows for timely tool replacement, ensuring consistent product quality.
Aerospace Industry
Wear on aircraft components can compromise safety and reliability. Monitoring wear on critical parts like turbine blades and landing gear is essential for preventing failures.
Automotive Industry
Wear on engine components like pistons and valves can reduce fuel efficiency and increase emissions. Regular inspection and maintenance based on wear measurements can improve engine performance and longevity.
As you can see, proper maintenance is key. Consider investing in Best Dartboard Lighting Systems to better see the condition of your dart equipment.
Conclusie
Point wear measurement is an essential practice for maintaining optimal performance, extending lifespan, and ensuring safety across various applications. By understanding the different methods of measurement, the factors affecting wear, and the available preventative measures, you can make informed decisions to minimize wear and maximize the value of your tools and equipment. Implementing a proactive approach to wear management will result in improved efficiency, reduced downtime, and significant cost savings. Therefore, prioritize regular inspections and preventative maintenance to mitigate the effects of point wear. Invest in proper measurement tools and techniques, and don’t hesitate to seek expert advice to optimize your wear management strategies. Start today to protect your investments and ensure long-term success.
Hoi, Ik ben Dieter, En ik heb Dartcounter gemaakt (Dartcounterapp.com). Mijn motivatie was geen darts -expert - helemaal tegenovergestelde! Toen ik voor het eerst begon te spelen, Ik hield van het spel, maar vond het moeilijk en afleidend om nauwkeurige scores te houden en statistieken te volgen.
Ik dacht dat ik niet de enige kon zijn die hiermee worstelde. Dus, Ik besloot om een oplossing te bouwen: een eenvoudig te gebruiken applicatie die iedereen, Ongeacht hun ervaringsniveau, zou kunnen gebruiken om moeiteloos te scoren.
Mijn doel voor Dartcounter was eenvoudig: Laat de app de nummers afhandelen - het scoren, de gemiddelden, de statistieken, Zelfs checkout suggesties - zodat spelers puur kunnen richten op hun worp en genieten van het spel. Het begon als een manier om het probleem van mijn eigen beginners op te lossen, En ik ben heel blij dat het is uitgegroeid tot een nuttig hulpmiddel voor de bredere darts -community.