The key to a leak-free system often hinges on proper O-ring installation. This O-ring installation guide provides a comprehensive breakdown of the steps, ensuring a secure and reliable seal. You’ll learn about choosing the right O-ring, preparing the surfaces, and mastering various installation techniques to prevent damage and ensure optimal performance.
Still Using Pen & Paper (or a Chalkboard)?! 
Step into the future! The Dart Counter App handles all the scoring, suggests checkouts, and tracks your stats automatically. It's easier than you think!
Try the Smart Dart Counter App FREE!Ready for an upgrade? Click above!
Choosing the Right O-Ring for Your Application
Before diving into the O-ring installation process, selecting the correct O-ring material and size is paramount. Consider factors like:
- Fluid Compatibility: Ensure the O-ring material is compatible with the fluid it will be sealing. Incompatible fluids can cause swelling, degradation, or premature failure.
- Temperature Range: O-rings have specific temperature ranges within which they maintain their sealing properties. Exceeding these limits can compromise the seal.
- Pressure Requirements: High-pressure applications require O-rings made from materials that can withstand the pressure without extruding or deforming.
- Size and Dimensions: Accurate measurements of the groove and gland are crucial for selecting the correct O-ring size. Undersized O-rings may leak, while oversized ones can be difficult to install and prone to damage.
Using the wrong O-ring material or size can lead to immediate or eventual failure, resulting in leaks and potential system damage. Always consult manufacturer specifications and material compatibility charts before selecting an O-ring.
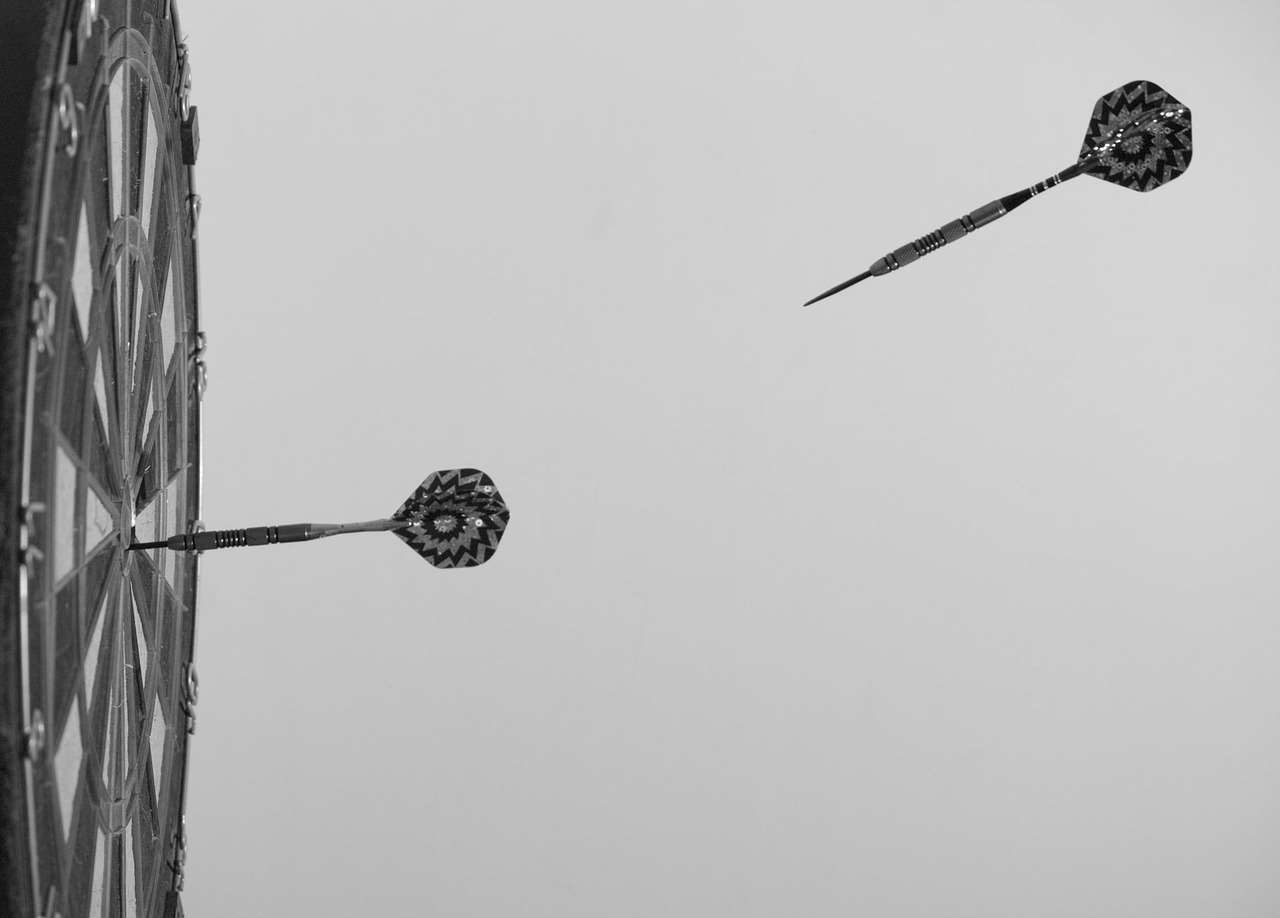
Preparing for O-Ring Installation: A Clean Slate
Proper preparation is essential for a successful O-ring installation. This involves cleaning the gland and the O-ring itself to remove any contaminants that could compromise the seal. Use a lint-free cloth and a compatible cleaning solvent to wipe down both surfaces. Inspect the gland for any burrs, sharp edges, or imperfections that could damage the O-ring during installation. These should be removed or smoothed out before proceeding.
Surface Finish Matters
The surface finish of the gland is crucial for proper sealing. A rough surface can create leak paths, while a surface that is too smooth may not allow the O-ring to grip effectively. Aim for a surface finish that is smooth but not polished. Using a specialized Choose Best Dart Equipment for deburring can also help with preparing the surface.
Carefully inspect the O-ring for any defects, such as cuts, nicks, or imperfections. Discard any damaged O-rings, as they will not provide a reliable seal. Consider using an O-ring lubricant to aid in installation and prevent damage. Ensure the lubricant is compatible with the O-ring material and the fluid it will be sealing.
O-Ring Installation Techniques: Mastering the Process
Several O-ring installation techniques can be employed, depending on the application and the size of the O-ring. Here are a few common methods:
- Manual Installation: For smaller O-rings, manual installation is often the simplest method. Gently stretch the O-ring and work it into the gland, ensuring it is seated properly. Avoid twisting or pinching the O-ring during installation, as this can cause damage.
- Cone Installation: For larger O-rings or those that are difficult to stretch, a cone-shaped tool can be used to guide the O-ring into the gland. The cone helps to evenly distribute the stretching force, reducing the risk of damage.
- Expanding Mandrel: An expanding mandrel can be used to stretch the O-ring over a shaft or piston. This method is particularly useful for installing O-rings in dynamic sealing applications.
Regardless of the technique used, take your time and be careful not to damage the O-ring during installation. Using the appropriate tools and techniques will greatly increase your chances of a successful seal. Consider related keywords such as O-ring seal, rubber O-ring, O-ring size chart, and how to install an O-ring when searching for specific information.
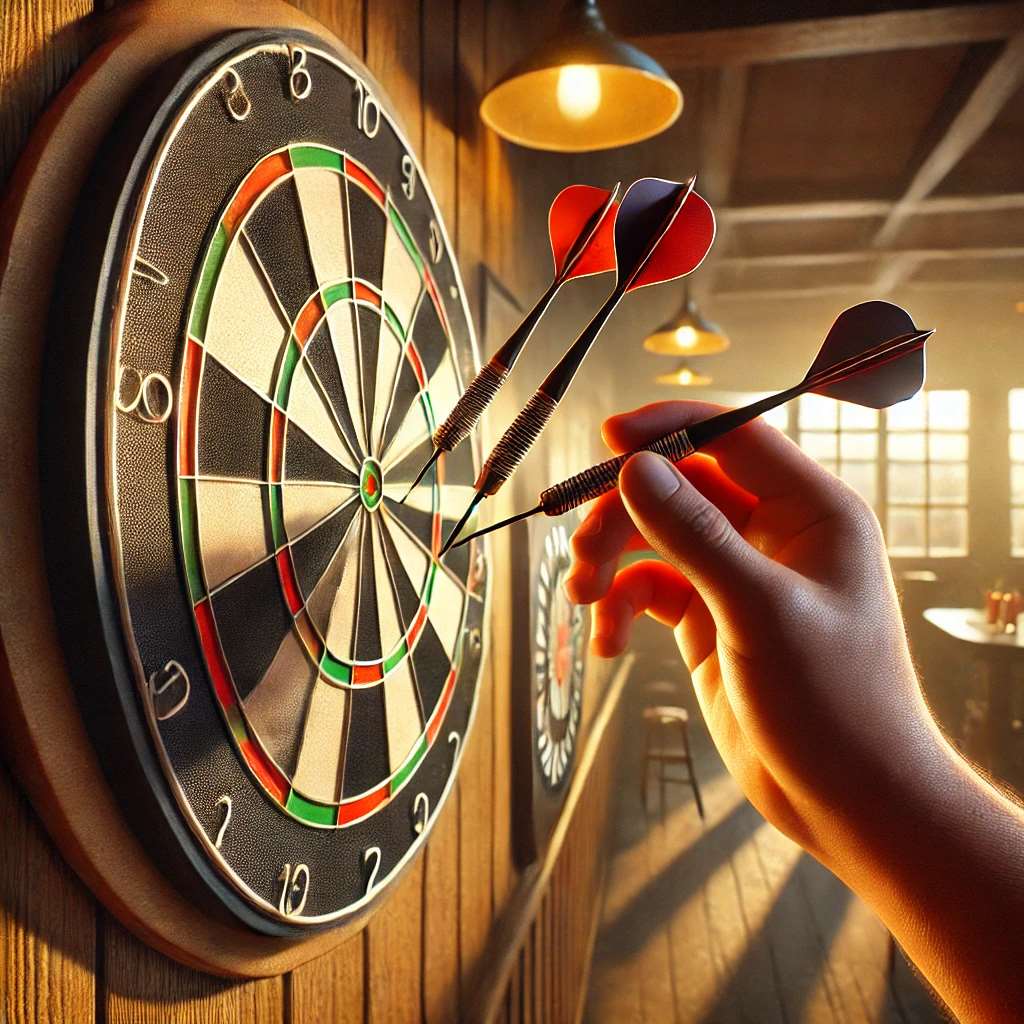
Lubrication: A Key Component of O-Ring Installation
O-ring lubricant plays a crucial role in ensuring a successful installation and extending the lifespan of the seal. A proper lubricant reduces friction, making it easier to install the O-ring without damage. It also helps to protect the O-ring from abrasion and wear during operation. When choosing a lubricant, it’s essential to consider:
- Compatibility: The lubricant must be compatible with both the O-ring material and the fluid being sealed. Incompatible lubricants can cause swelling, degradation, or other damage to the O-ring.
- Temperature Range: The lubricant should be able to withstand the operating temperature range of the application without breaking down or losing its lubricating properties.
- Viscosity: The viscosity of the lubricant should be appropriate for the application. A lubricant that is too thick may be difficult to apply, while one that is too thin may not provide adequate lubrication.
Apply a thin, even coat of lubricant to the O-ring and the gland before installation. Avoid using excessive lubricant, as this can attract contaminants and create leak paths.
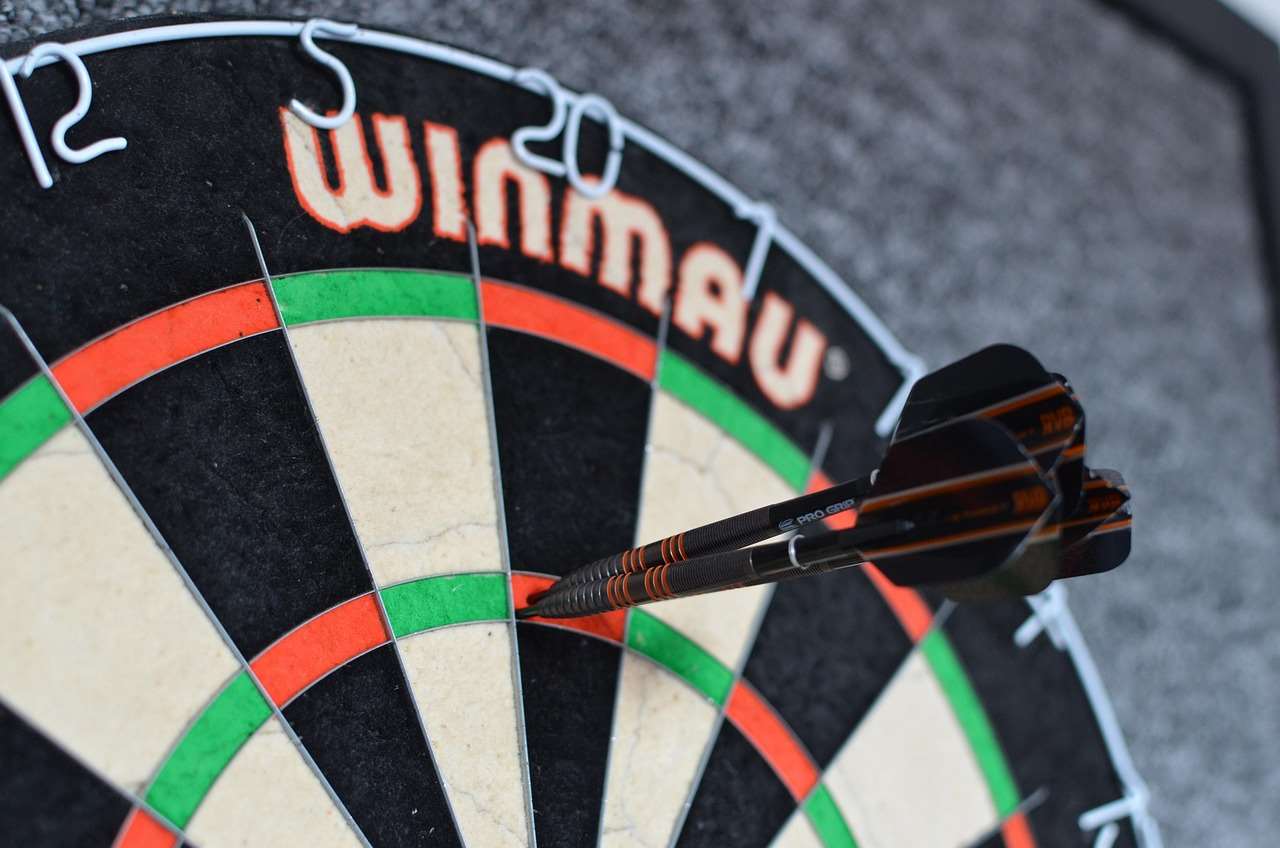
Troubleshooting Common O-Ring Installation Problems
Even with careful preparation and proper techniques, O-ring installation problems can sometimes occur. Here are some common issues and how to address them:
- O-Ring Pinching: Pinching occurs when the O-ring is squeezed between the mating surfaces during assembly. This can damage the O-ring and create a leak path. To prevent pinching, ensure the gland is properly designed and that the O-ring is not too large.
- O-Ring Twisting: Twisting can occur when the O-ring is installed unevenly or when the mating surfaces are not aligned. This can distort the O-ring and compromise the seal. To prevent twisting, use a cone-shaped tool or an expanding mandrel to guide the O-ring into the gland.
- O-Ring Extrusion: Extrusion occurs when the O-ring is forced into the gap between the mating surfaces under high pressure. This can damage the O-ring and cause it to fail prematurely. To prevent extrusion, use a harder O-ring material or reduce the gap size.
If you encounter any of these problems, stop and reassess the situation. Do not force the O-ring into place, as this will likely cause further damage. By carefully diagnosing the problem and taking corrective action, you can ensure a successful O-ring installation.
Dynamic vs. Static O-Ring Installation
The method used for O-ring installation can vary slightly depending on whether the application is static or dynamic. In a **static application**, the O-ring is compressed between two surfaces that do not move relative to each other. In a **dynamic application**, the O-ring is used to seal between surfaces that move relative to each other, such as a piston and cylinder. Dynamic applications require different considerations. Ensuring smooth surface finishes and adequate lubrication is even more critical to minimize friction and wear.
For dynamic seals, choose O-ring materials that are resistant to abrasion and wear. Proper lubrication is also essential to reduce friction and extend the lifespan of the seal. Inspect the O-ring regularly for signs of wear and replace it as needed. Knowing the What Makes Darts Premium Quality for your dart equipment can sometimes be analogous to the same level of scrutiny for O-ring choice.
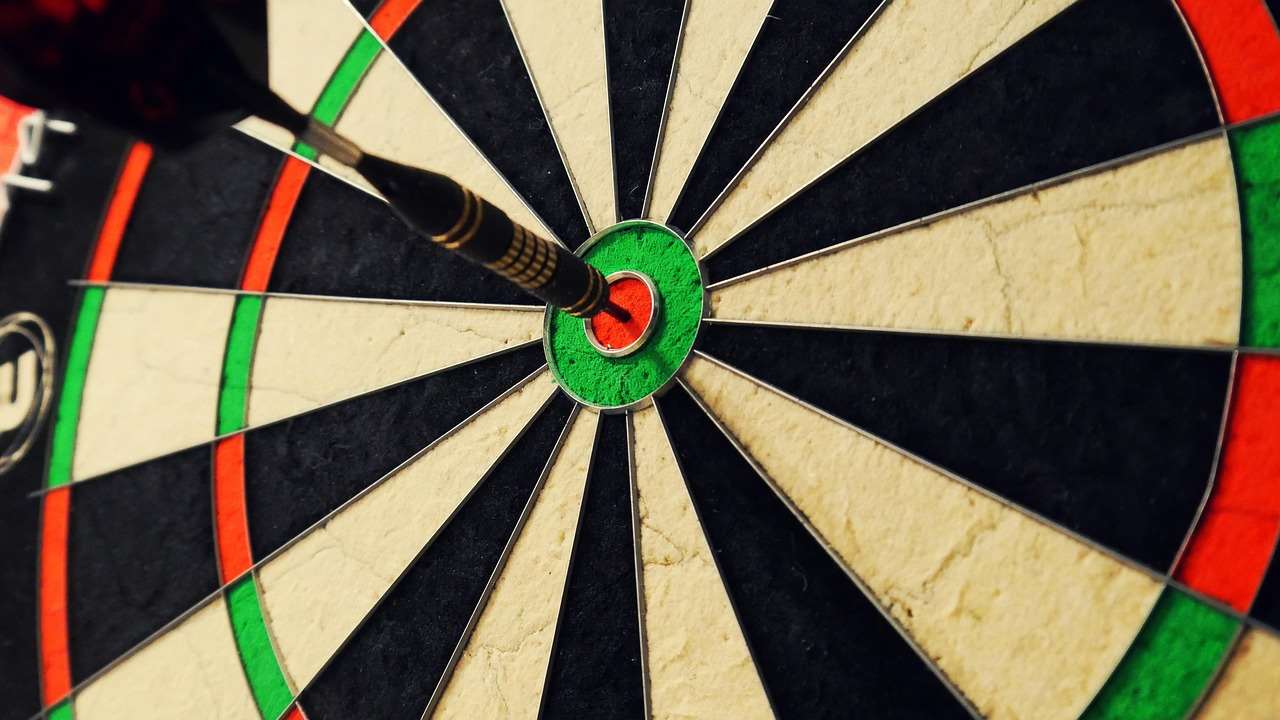
Advanced O-Ring Installation Considerations
For more complex applications, consider these advanced considerations for O-ring installation:
- Vacuum Applications: Vacuum applications require O-rings with low outgassing properties to prevent contamination of the vacuum environment.
- High-Temperature Applications: High-temperature applications require O-rings made from materials that can withstand the extreme temperatures without degrading.
- Chemical Resistance: Applications involving harsh chemicals require O-rings made from materials that are resistant to the specific chemicals being used.
Consult with an O-ring specialist to determine the best material and installation techniques for your specific application. For advanced material science, research fluoroelastomer O-rings, nitrile rubber O-rings, and silicone O-rings to understand their respective chemical and temperature resistances.

The Importance of Regular O-Ring Maintenance and Inspection
Even with proper O-ring installation, regular maintenance and inspection are crucial for ensuring long-term performance and preventing leaks. Inspect O-rings periodically for signs of wear, damage, or degradation. Replace O-rings as needed, following the same installation procedures outlined above. Maintaining proper records of O-ring replacements can help you track performance and identify potential problems early on. Using high-quality O-rings and following best practices for installation and maintenance will help ensure a leak-free system and minimize downtime. To ensure quality, consider Quality Comparison Budget Premium Darts and extend the same mindset to your O-ring selection process.
Conclusion: Mastering the Art of O-Ring Installation
Proper O-ring installation is vital for ensuring reliable sealing and preventing costly leaks. By selecting the right O-ring material, preparing the surfaces properly, using the appropriate installation techniques, and performing regular maintenance, you can maximize the lifespan and performance of your O-rings. Remember to always consult manufacturer specifications and seek professional advice when needed. Explore our other helpful guides to learn more about related topics. Ready to upgrade your equipment? Buying Guide Budget Premium Dart Sets can also help with your next purchase.