De toekomst van darts manufacturing hinges on adapting to sustainable practices and embracing technological advancements; this means prioritizing eco-friendly materials and automating production to meet rising demand while minimizing environmental impact. This article explores the key darts manufacturing future challenges, including material sourcing, production efficiency, and market trends, offering insights into how manufacturers can thrive in a rapidly evolving landscape.
⚠️ Still Using Pen & Paper (Of een schoolbord)?! ⚠️
Stap in de toekomst! De Dart Teller -app behandelt alle scoren, stelt kassa voor, en volgt uw statistieken automatisch. It's easier than you think!
Probeer de Smart Dart Teller -app gratis!Klaar voor een upgrade? Klik hierboven!
Navigating Material Sourcing and Sustainability: Key Darts Manufacturing Future Challenges
One of the most pressing darts manufacturing future challenges revolves around material sourcing and sustainability. Traditioneel, darts have relied heavily on materials like tungsten, messing, and steel. While durable, these materials often come with environmental consequences related to mining and processing. The industry is now facing increasing pressure to adopt more sustainable alternatives.
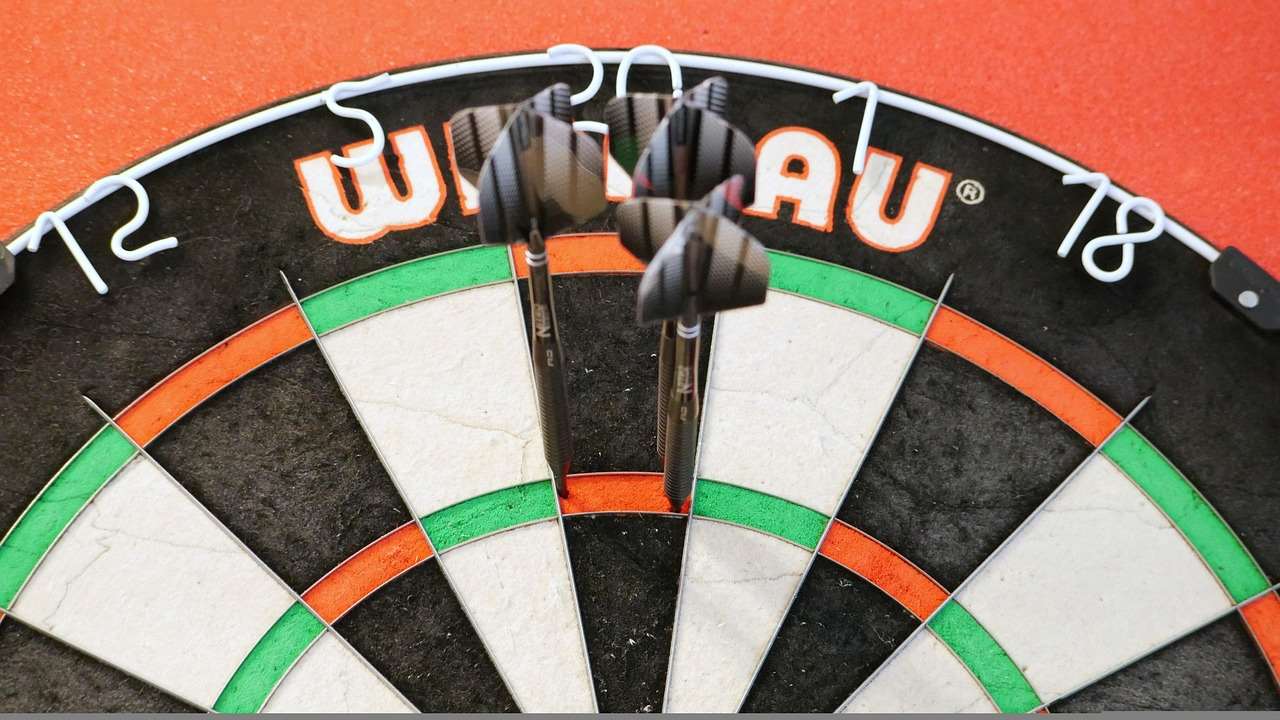
Alternative materials are being explored, including recycled metals, bio-plastics, and even innovative composite materials. The challenge lies in finding materials that offer comparable performance characteristics – weight, density, and durability – while minimizing their environmental footprint. This requires significant research and development efforts, as well as collaboration with material scientists and engineers.
Embracing Eco-Friendly Materials
Switching to eco-friendly materials is not just about ticking a box; it’s about creating a more responsible and sustainable business model. Here are some actionable steps manufacturers can take:
- Conduct a Life Cycle Assessment (LCA): Evaluate the environmental impact of existing materials and processes.
- Explore Recycled Metals: Investigate the feasibility of using recycled tungsten, messing, or steel.
- Research Bio-Plastics: Consider bio-plastics derived from renewable resources for dart components.
- Collaborate with Suppliers: Work with suppliers who prioritize sustainable practices and offer certified materials.
Moreover, consumer awareness of environmental issues is growing. Brands that prioritize sustainability will likely gain a competitive edge and attract environmentally conscious customers. Begrip Business of Darts is critical to adapt to the new landscape.
The Rise of Automation and Precision Manufacturing
Another significant hurdle in overcoming darts manufacturing future challenges is the need to improve production efficiency through automation and precision manufacturing techniques. Traditional darts manufacturing often involves manual labor, which can be time-consuming and prone to errors. Embracing automation can lead to increased output, reduced costs, and improved product quality.
Automated manufacturing processes can streamline various stages of dart production, from material cutting and shaping to assembly and finishing. Computer Numerical Control (CNC) machines, robotic arms, and automated inspection systems can enhance precision and consistency, ensuring that each dart meets exacting specifications. This is especially crucial for high-end darts where even minor variations can affect performance.
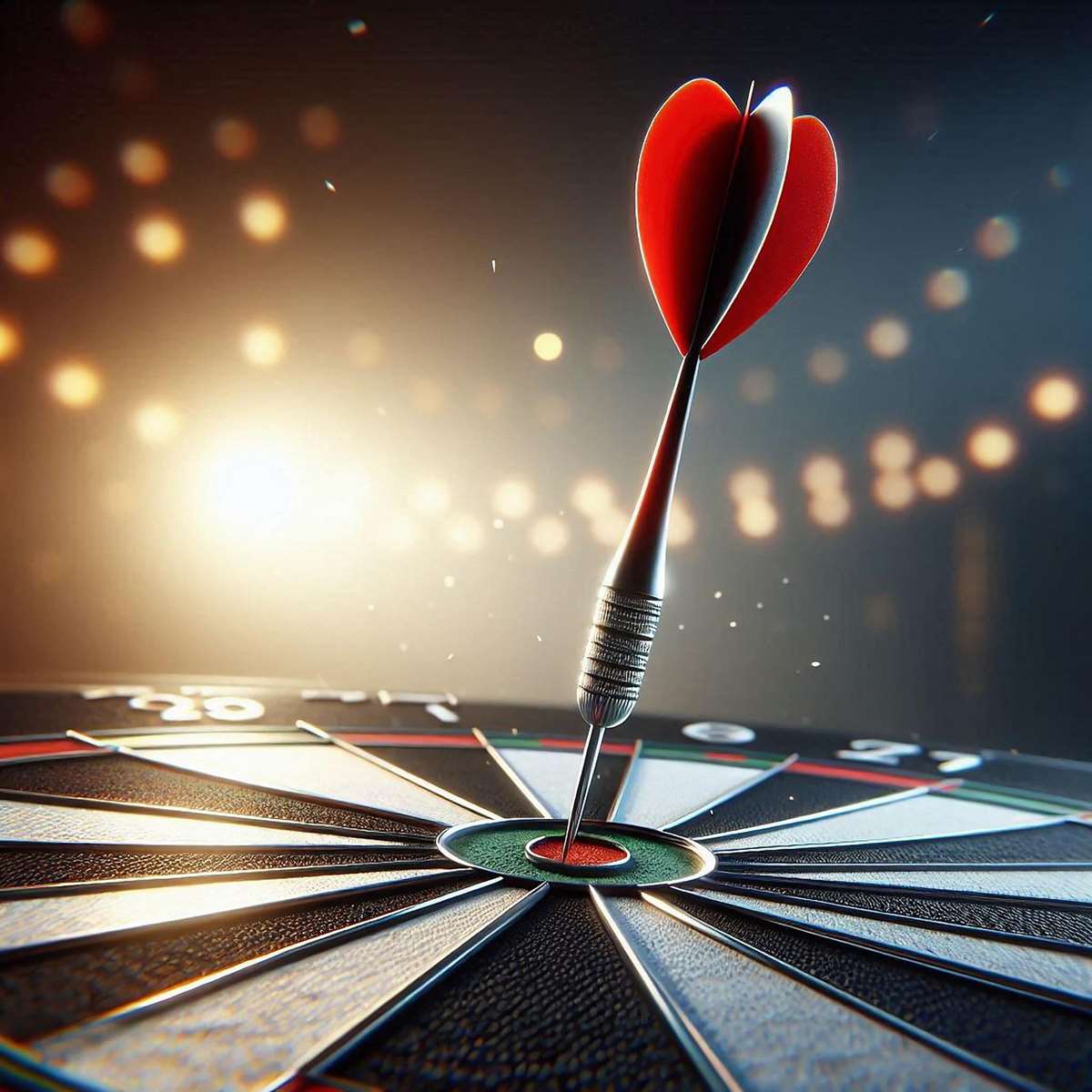
Benefits of Automation in Darts Manufacturing
Investing in automation offers several key benefits:
- Increased Production Capacity: Automation can significantly increase the number of darts produced per day.
- Reduced Labor Costs: While initial investment costs may be high, automation can lower long-term labor expenses.
- Improved Product Quality: Automated processes minimize human error and ensure consistent quality.
- Enhanced Precision: CNC machines and other automated tools offer unparalleled precision in manufacturing.
Echter, implementing automation also presents challenges. Manufacturers need to invest in new equipment, train their workforce, and adapt their production processes. A phased approach, starting with automating the most repetitive and labor-intensive tasks, may be the most practical strategy.
Adapting to Changing Market Trends and Consumer Preferences
Darts manufacturing future challenges are not just about production processes; they also involve understanding and adapting to changing market trends and consumer preferences. The darts market is dynamic, with evolving demands for different types of darts, materials, and designs. Manufacturers need to stay ahead of these trends to remain competitive.
Consumer preferences are influenced by various factors, including professional dart players, online communities, and social media. Manufacturers should actively monitor these channels to identify emerging trends and tailor their products accordingly. Bijvoorbeeld, there’s growing demand for darts with unique grip patterns, customized designs, and innovative technologies like embedded sensors.
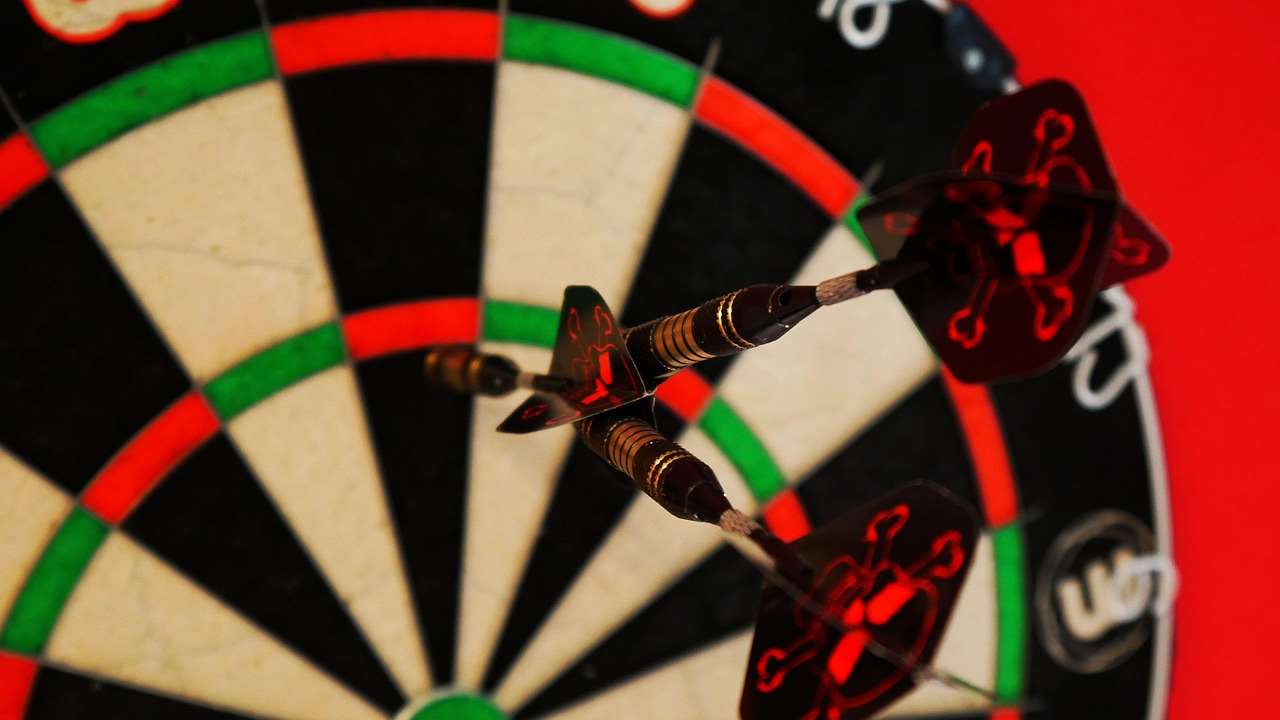
Meeting the Demands of the Modern Dart Player
To cater to the evolving needs of dart players, manufacturers can focus on the following:
- Offer a Wide Range of Darts: Provide darts with different weights, shapes, and materials to suit various playing styles.
- Customization Options: Allow customers to personalize their darts with custom engravings, grip patterns, or colors.
- Incorporate Technology: Explore the integration of sensors and data analytics to provide players with performance feedback.
- Engage with the Community: Participate in online forums, social media groups, and dart tournaments to gather feedback and build relationships.
Adapting to new consumer preferences, especially with the rise in online play, is key. Keep in mind Darts tv -rechtenwaarde is increasingly correlated with audience engagement.
The Impact of Global Supply Chains and Geopolitical Factors
The complexity of global supply chains introduces another layer to darts manufacturing future challenges. Manufacturers often rely on suppliers from different countries for raw materials, components, and manufacturing services. Geopolitical events, trade disputes, and economic fluctuations can disrupt these supply chains, leading to delays, increased costs, and uncertainty.
Diversifying supply chains is crucial for mitigating these risks. Manufacturers should avoid relying on a single supplier or country for critical materials and components. Building relationships with multiple suppliers in different regions can provide a buffer against disruptions. Aanvullend, investing in local sourcing can reduce reliance on global supply chains and support local economies.
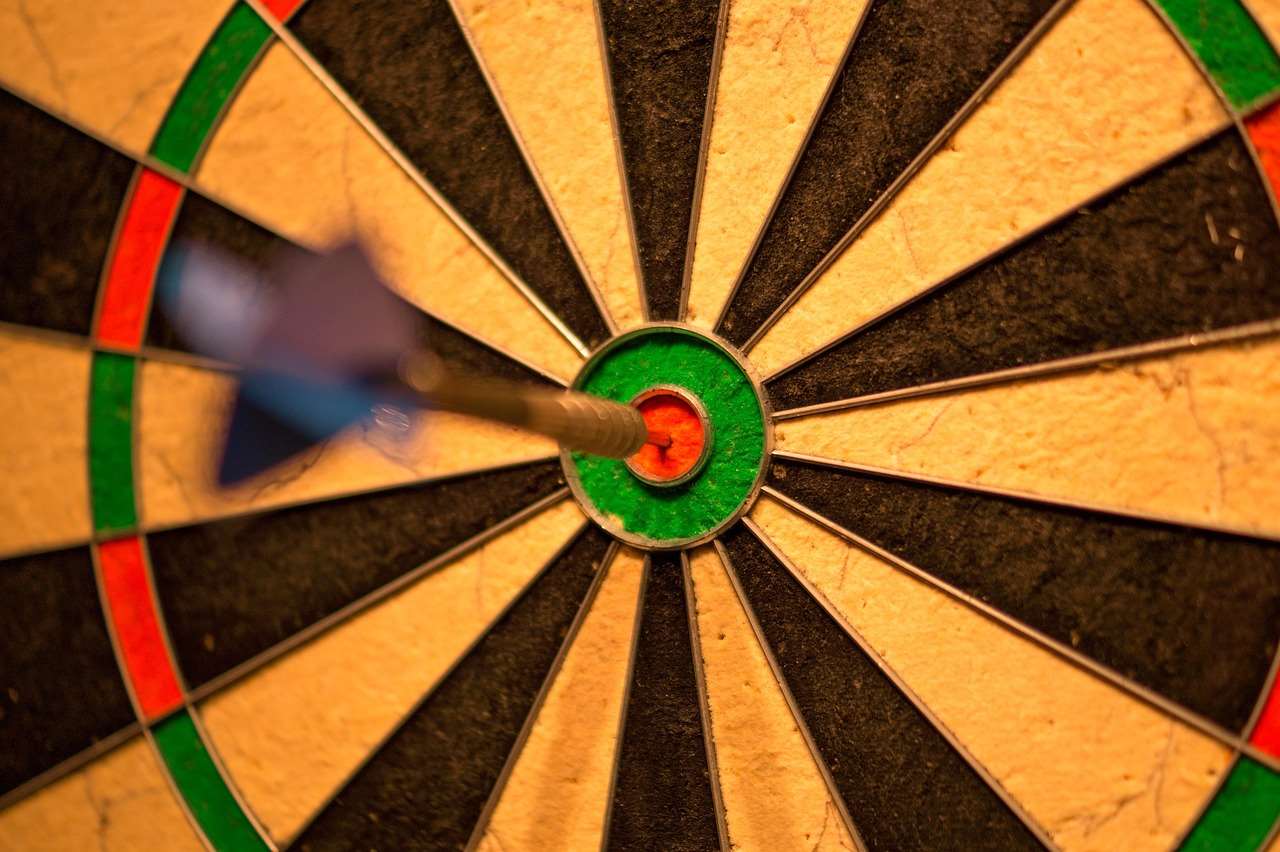
Strategies for Strengthening Supply Chains
Here are some strategies manufacturers can implement to strengthen their supply chains:
- Develop Multiple Suppliers: Establish relationships with several suppliers for each critical material and component.
- Invest in Local Sourcing: Explore opportunities to source materials and components from domestic suppliers.
- Implement Inventory Management Systems: Use technology to track inventory levels and anticipate potential shortages.
- Monitor Geopolitical Risks: Stay informed about global events and trade policies that could impact supply chains.
Effective risk management and proactive planning are essential for navigating the challenges of global supply chains. Manufacturers must be prepared to adapt to changing circumstances and mitigate potential disruptions.
The Role of Research and Development in Innovation
Overcoming darts manufacturing future challenges requires a strong commitment to research and development (R&D). Investing in R&D is essential for developing new materials, improving production processes, and creating innovative products. Manufacturers who prioritize R&D will be better positioned to adapt to changing market trends and maintain a competitive edge.
R&D efforts should focus on exploring new materials, optimizing dart designs, and incorporating advanced technologies. This could involve collaborating with universities, research institutions, and technology companies. Verder, manufacturers should encourage innovation within their own organizations by fostering a culture of experimentation and providing resources for employees to pursue new ideas.
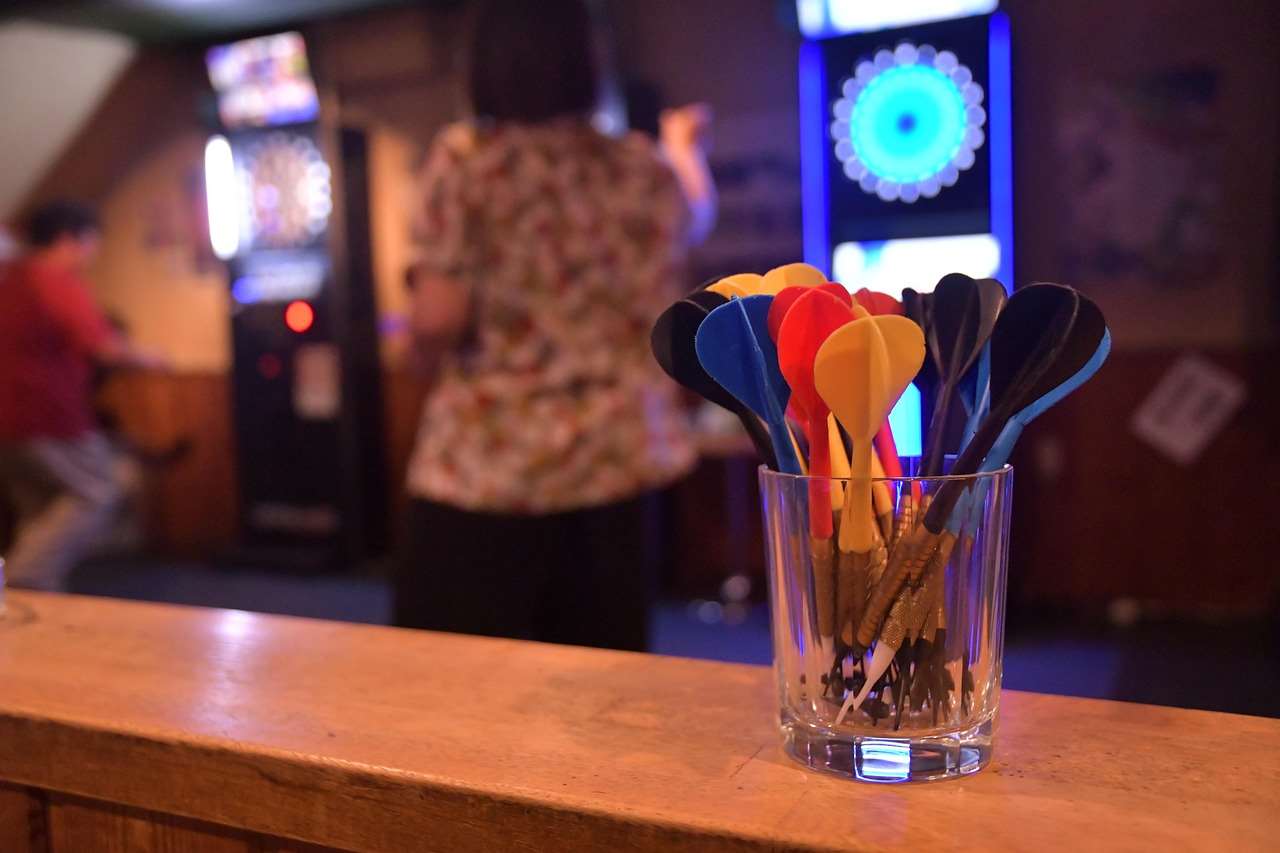
Prioritizing Innovation in Darts Manufacturing
Here are some ways manufacturers can prioritize innovation:
- Invest in R&D: Allocate resources to research and development projects.
- Collaborate with Experts: Partner with universities, research institutions, and technology companies.
- Foster a Culture of Innovation: Encourage employees to experiment and pursue new ideas.
- Protect Intellectual Property: Secure patents and trademarks for innovative products and processes.
By prioritizing R&D, manufacturers can create a pipeline of innovative products that meet the evolving needs of dart players and drive growth in the industry.
Addressing Skills Gaps and Workforce Development
Another critical aspect of addressing darts manufacturing future challenges is ensuring a skilled workforce. As manufacturing processes become more automated and complex, there’s a growing need for skilled technicians, engineers, and operators. Manufacturers need to invest in workforce development programs to bridge the skills gap and prepare employees for the jobs of the future.
Workforce development programs can include apprenticeship programs, on-the-job training, and partnerships with vocational schools and community colleges. These programs should focus on developing skills in areas such as CNC programming, robotics maintenance, and data analytics. Aanvullend, manufacturers should provide opportunities for employees to upgrade their skills and stay current with the latest technologies.
Investing in Workforce Development
Here are some strategies manufacturers can use to invest in workforce development:
- Establish Apprenticeship Programs: Partner with local schools and offer apprenticeship programs to train the next generation of manufacturing workers.
- Provide On-the-Job Training: Offer on-the-job training to help employees develop new skills and advance their careers.
- Partner with Educational Institutions: Collaborate with vocational schools and community colleges to develop customized training programs.
- Offer Tuition Reimbursement: Provide tuition reimbursement for employees who pursue relevant education or training.
By investing in workforce development, manufacturers can ensure they have the skilled workforce they need to meet the challenges of the future and remain competitive in the global marketplace. De Hoe Darts Media Deals werkt are often impacted by having a compelling product and manufacturing expertise.
Conclusie
Successfully navigating the darts manufacturing future challenges requires a proactive and adaptable approach. By prioritizing sustainable materials, embracing automation, understanding market trends, strengthening supply chains, investing in R&D, and developing a skilled workforce, manufacturers can position themselves for long-term success. The future of darts manufacturing lies in innovation, sustainability, and a commitment to meeting the evolving needs of dart players worldwide. By embracing these principles, manufacturers can not only overcome the challenges they face but also drive growth and innovation in the industry. Are you ready to take the next step and implement these strategies in your darts manufacturing process? Reach out to industry experts and begin transforming your approach today.
Hoi, Ik ben Dieter, En ik heb Dartcounter gemaakt (Dartcounterapp.com). Mijn motivatie was geen darts -expert - helemaal tegenovergestelde! Toen ik voor het eerst begon te spelen, Ik hield van het spel, maar vond het moeilijk en afleidend om nauwkeurige scores te houden en statistieken te volgen.
Ik dacht dat ik niet de enige kon zijn die hiermee worstelde. Dus, Ik besloot om een oplossing te bouwen: een eenvoudig te gebruiken applicatie die iedereen, Ongeacht hun ervaringsniveau, zou kunnen gebruiken om moeiteloos te scoren.
Mijn doel voor Dartcounter was eenvoudig: Laat de app de nummers afhandelen - het scoren, de gemiddelden, de statistieken, Zelfs checkout suggesties - zodat spelers puur kunnen richten op hun worp en genieten van het spel. Het begon als een manier om het probleem van mijn eigen beginners op te lossen, En ik ben heel blij dat het is uitgegroeid tot een nuttig hulpmiddel voor de bredere darts -community.