Producing high-quality darts consistently requires stringent **darts brand manufacturing process qc**. This article provides a comprehensive overview of the quality control measures implemented by leading darts brands to ensure their products meet the highest standards, covering everything from material selection to final inspection.
⚠️ Still Using Pen & Paper (Of een schoolbord)?! ⚠️
Stap in de toekomst! De Dart Teller -app behandelt alle scoren, stelt kassa voor, en volgt uw statistieken automatisch. It's easier than you think!
Probeer de Smart Dart Teller -app gratis!Klaar voor een upgrade? Klik hierboven!
Understanding the Importance of Quality Control in Darts Manufacturing
The seemingly simple dart undergoes a complex manufacturing process. Every stage, from the initial design to the packaging of the final product, significantly impacts the dart’s performance, durability, and overall feel. Poor quality control at any point can result in unbalanced darts, inconsistent grip, premature wear, en uiteindelijk, a negative experience for the player. This is why leading **darts brands** invest heavily in rigorous testing and inspection procedures. Moreover, consistent quality impacts brand reputation and customer loyalty.
Imagine a professional player relying on their equipment for their livelihood. A slight imperfection can be the difference between winning and losing. Even for recreational players, using well-made darts enhances enjoyment and allows for skill development. Therefore, **quality control is not just a process, it’s a commitment to providing the best possible product to the end user**. This dedication to quality is a hallmark of reputable darts brands.
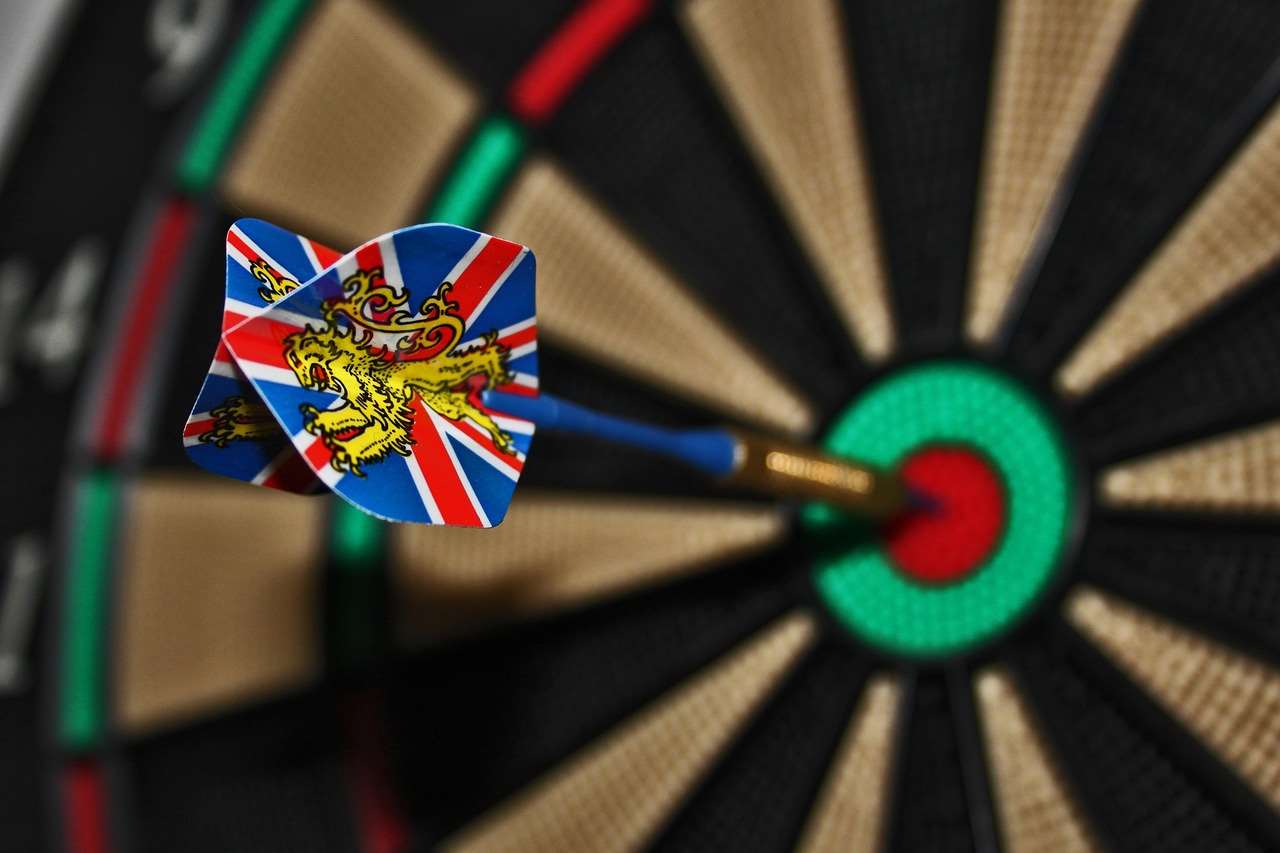
Key Stages of the Darts Brand Manufacturing Process
The **darts brand manufacturing process** can be broken down into several crucial stages, each requiring careful attention to detail and robust **QC** measures. Here’s a look at the typical steps involved:
- Design and Prototyping: This initial phase involves conceptualizing the dart’s design, including its shape, weight distribution, and grip features. Prototypes are created and tested extensively.
- Material Selection: The choice of materials significantly impacts the dart’s performance and durability. Tungsten alloys are commonly used for the barrel due to their high density. Flights are often made from plastic, nylon or other synthetic materials.
- Barrel Manufacturing: The barrel is the heart of the dart. It is usually made through machining, using Computer Numerical Control (CNC) machines.
- Grip Machining: Intricate grip patterns are machined into the barrel to provide optimal control.
- Point Attachment: The dart point is securely attached to the barrel, often using a specialized press-fit or thread.
- Shaft and Flight Assembly: The shaft, which connects the barrel to the flight, is attached, and the flights are assembled to the shaft.
- Final Inspection and Packaging: Each dart is meticulously inspected for any defects or inconsistencies before being packaged.
Material Selection: Setting the Foundation for Quality
The type and quality of materials used significantly determine the darts’ performance and longevity. Tungsten is a popular choice for dart barrels due to its high density, which allows for a slimmer profile and closer groupings on the board. Echter, not all tungsten is created equal. **Leading darts brands** source high-grade tungsten alloys to ensure consistency and durability. Alternative materials include brass and nickel-silver, usually in lower cost darts. The specific material used impacts the overall economic benefits hosting darts event.
Flights are typically made from plastic, nylon, or other synthetic materials. The quality of these materials affects the flight’s durability and aerodynamic properties. Cheaper materials may tear or deform easily, impacting the dart’s flight path.
Quality Control Measures Throughout the Manufacturing Process
Effective **darts brand manufacturing process qc** isn’t just a final check; it’s integrated into every stage. Here are some key areas where quality control measures are implemented:
- Raw Material Inspection: Incoming raw materials are inspected to ensure they meet specified standards for composition, purity, and dimensions. Bijvoorbeeld, tungsten alloy bars are tested for their tungsten content.
- In-Process Inspection: During each manufacturing stage, parts are inspected for dimensional accuracy, surface finish, and any other critical parameters. CNC machines are regularly calibrated to maintain precision.
- Functional Testing: Prototypes and finished darts are subjected to functional testing to evaluate their performance. This may include throw tests, balance checks, and durability testing.
- Statistical Process Control (SPC): SPC techniques are used to monitor and control the manufacturing process, identifying and addressing any variations or trends that could lead to defects.
- Final Inspection: Before packaging, each dart is thoroughly inspected for any visual defects, dimensional inaccuracies, or functional issues. This may involve manual inspection or automated vision systems.
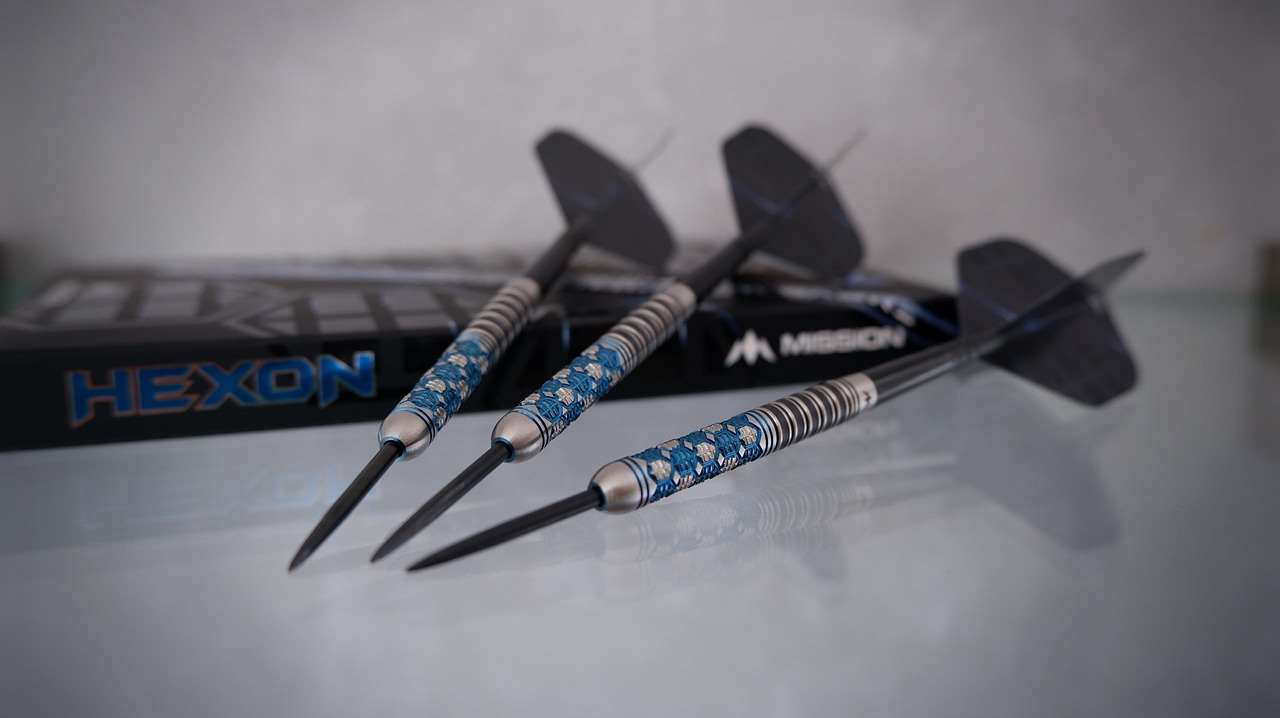
Dimensional Accuracy: Ensuring Consistent Performance
Dimensional accuracy is crucial for dart performance. Even slight variations in the barrel’s diameter, length, or weight can affect its flight characteristics. **Darts brands** use precision measuring instruments, such as calipers and micrometers, to ensure that all parts meet specified dimensions. Verder, CNC machining ensures consistent results, minimizing the risk of human error.
Weight consistency is also paramount. A set of darts should ideally have the same weight, within a tight tolerance. **QC** procedures often include weighing each dart individually and rejecting any that fall outside the acceptable range. Inconsistencies can impact players’ throwing consistency and scores.
The dimensions of the shaft and flight also impact accuracy. Variations in these elements can negatively impact the darts performance.
Tools and Technologies Used in Darts Quality Control
**Modern darts brand manufacturing process qc** relies on a range of sophisticated tools and technologies. These tools help ensure accuracy, consistency, and efficiency in the manufacturing process.
- Coordinate Measuring Machines (CMMs): CMMs are used to precisely measure the dimensions of complex parts, ensuring they meet specified tolerances.
- Optical Comparators: Optical comparators project a magnified image of a part onto a screen, allowing for detailed inspection of its shape and dimensions.
- CNC Machines: Computer Numerical Control (CNC) machines are used to automate the machining process, ensuring consistent and accurate results. Regular calibration and maintenance are crucial for maintaining their precision.
- Automated Vision Systems: Automated vision systems use cameras and image processing software to automatically inspect parts for defects.
- Weight Scales: High-precision weight scales are used to ensure that each dart meets specified weight requirements.
The level of technology utilized often indicates the brand’s commitment to quality. Investing in advanced equipment shows that the brand values precision and consistency.
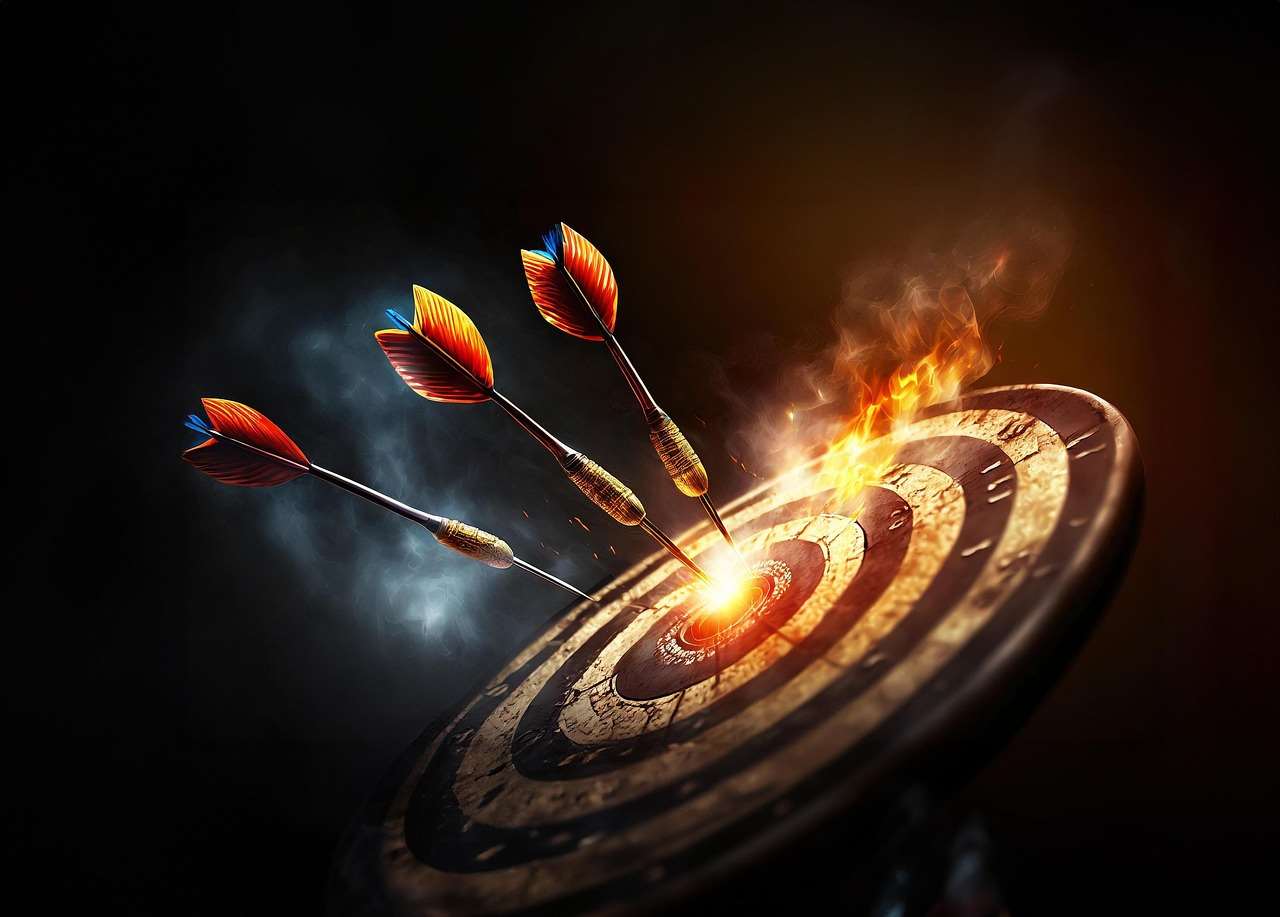
The Role of Skilled Technicians in Quality Assurance
While technology plays a vital role, skilled technicians are essential for effective **darts brand manufacturing process qc**. These technicians are responsible for operating and maintaining equipment, interpreting data, and identifying and resolving any quality issues. They are also responsible for training new employees on quality control procedures.
These professionals require a deep understanding of the manufacturing process, materials science, and quality control principles. Their expertise is crucial for ensuring that all products meet the highest standards. In many cases, they are involved in developing and implementing new quality control procedures.
Investing in employee training and development is a crucial part of any comprehensive quality control program. A well-trained workforce is more likely to identify and prevent quality problems.
Addressing Common Manufacturing Defects in Darts
Even with robust quality control measures, manufacturing defects can still occur. Here are some common defects found in darts and how **darts brands** address them:
- Dimensional Inaccuracies: Deviations from specified dimensions can affect the dart’s flight characteristics and balance. This can be prevented by careful attention to CNC machine calibration and in-process inspection.
- Surface Defects: Scratches, dents, or other surface imperfections can affect the dart’s grip and appearance. This can be minimized by careful handling and surface finishing processes.
- Weight Variations: Inconsistent weight within a set of darts can affect the player’s throwing consistency. This can be addressed by using high-precision weight scales and carefully monitoring the weight of each dart.
- Loose Points: A loose dart point can be dangerous and affect the dart’s accuracy. This can be prevented by using a secure attachment method and carefully inspecting each dart point.
- Flight Tears and Damage: Fragile or poorly made flights can impact the overall quality.
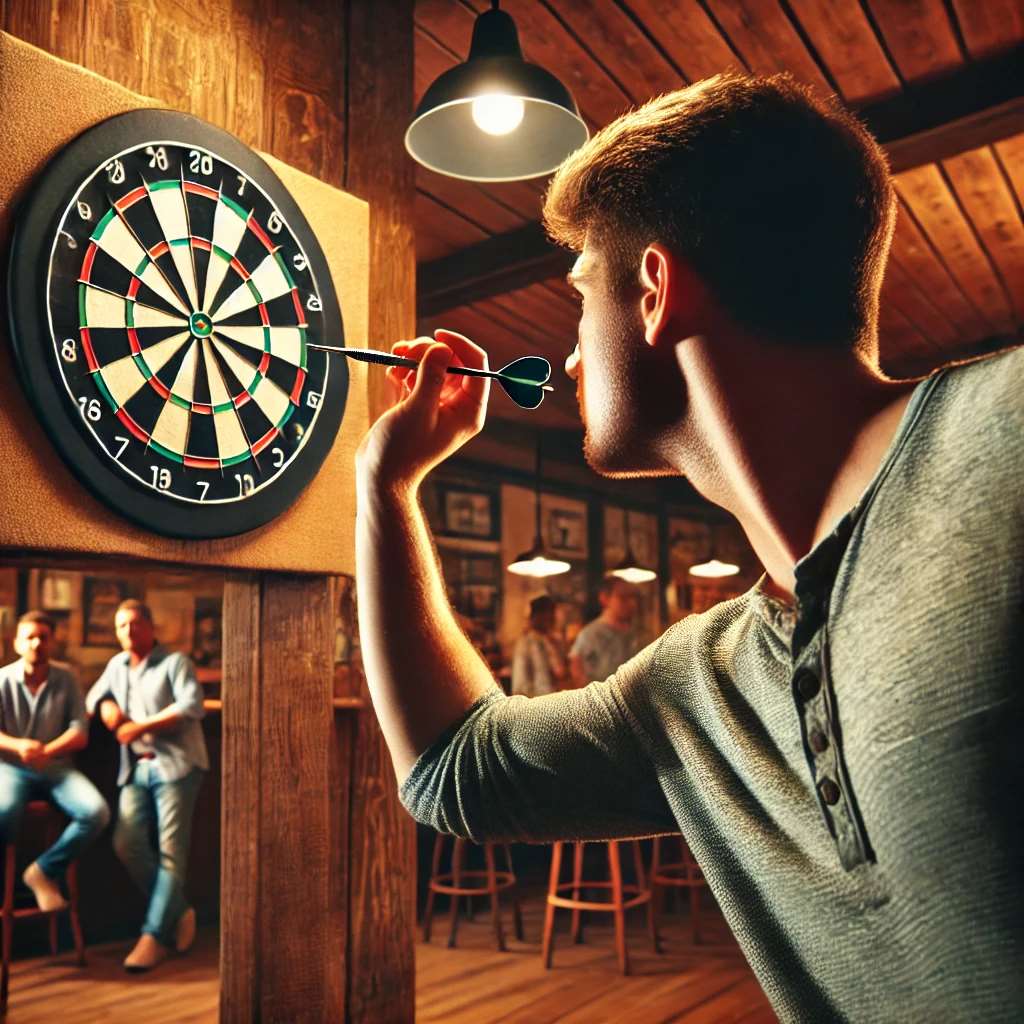
Continuous Improvement in Darts Manufacturing QC
Leading **darts brands** are committed to continuous improvement in their manufacturing processes and **QC** procedures. This involves regularly reviewing and updating processes to identify and eliminate sources of variation and improve overall quality. This dedication extends to the darts tourism boost local area.
This dedication often includes implementing statistical process control (SPC) techniques to monitor and control the manufacturing process. SPC helps identify and address any trends or variations that could lead to defects. Brands may also solicit feedback from players and retailers to identify areas for improvement.
By embracing a culture of continuous improvement, **darts brands** can ensure that their products consistently meet the highest standards of quality and performance.
The Impact of Quality Control on Brand Reputation and Customer Loyalty
Effective **darts brand manufacturing process qc** has a direct impact on brand reputation and customer loyalty. Customers are more likely to trust and purchase products from a brand that consistently delivers high-quality products. Word-of-mouth referrals and positive online reviews can significantly boost a brand’s reputation. This can directly impact how darts events help pubs bars.
Omgekeerd, poor quality control can damage a brand’s reputation and lead to customer dissatisfaction. Negative reviews and complaints can deter potential customers and damage the brand’s long-term viability.
Investing in quality control is an investment in the brand’s future. It demonstrates a commitment to providing customers with the best possible products and fostering long-term loyalty.
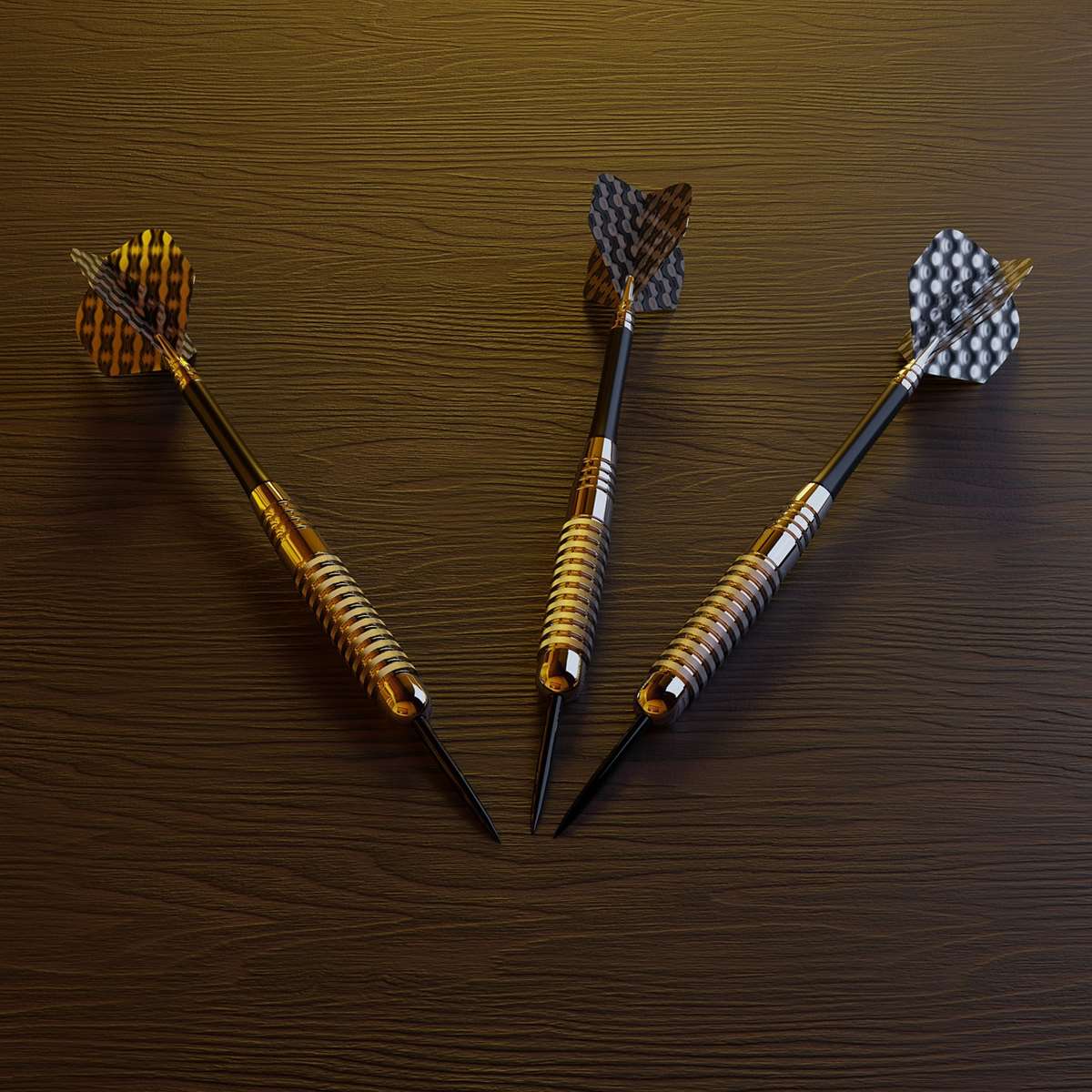
Choosing a Darts Brand with Strong Quality Control
When choosing a darts brand, consider their reputation for quality. Look for brands that invest in rigorous testing and inspection procedures. Read online reviews to see what other customers have to say about the brand’s products. A brand that clearly communicates its quality control practices is generally one you can trust.
Consider the materials used in the darts. High-quality materials, such as tungsten alloy, are more durable and perform better. Evaluate the craftsmanship of the darts. Look for clean lines, consistent finishes, and secure attachments.
By carefully evaluating these factors, you can choose a darts brand that provides high-quality products that enhance your playing experience.
Conclusie
In summary, **darts brand manufacturing process qc** is paramount for delivering consistent, high-performing darts. From meticulous material selection and in-process inspections to advanced technology and skilled technicians, every stage plays a crucial role. Choosing a brand with a strong commitment to quality ensures a better playing experience and fosters long-term customer loyalty. Uiteindelijk, quality control is not just a process, but a promise. Invest in quality darts and elevate your game!
Ready to upgrade your darts? Browse reputable brands and find the perfect set to improve your game today!
Hoi, Ik ben Dieter, En ik heb Dartcounter gemaakt (Dartcounterapp.com). Mijn motivatie was geen darts -expert - helemaal tegenovergestelde! Toen ik voor het eerst begon te spelen, Ik hield van het spel, maar vond het moeilijk en afleidend om nauwkeurige scores te houden en statistieken te volgen.
Ik dacht dat ik niet de enige kon zijn die hiermee worstelde. Dus, Ik besloot om een oplossing te bouwen: een eenvoudig te gebruiken applicatie die iedereen, Ongeacht hun ervaringsniveau, zou kunnen gebruiken om moeiteloos te scoren.
Mijn doel voor Dartcounter was eenvoudig: Laat de app de nummers afhandelen - het scoren, de gemiddelden, de statistieken, Zelfs checkout suggesties - zodat spelers puur kunnen richten op hun worp en genieten van het spel. Het begon als een manier om het probleem van mijn eigen beginners op te lossen, En ik ben heel blij dat het is uitgegroeid tot een nuttig hulpmiddel voor de bredere darts -community.