Flight ribbing explained simply, it’s the process of adding structural support to aircraft wings and control surfaces using ribs, which maintain the airfoil shape and distribute aerodynamic loads. This article will delve into the types of flight ribbing, their functions, construction methods, and importance in aircraft design and performance.
⚠️ Still Using Pen & Paper (or a Chalkboard)?! ⚠️
Step into the future! The Dart Counter App handles all the scoring, suggests checkouts, and tracks your stats automatically. It's easier than you think!
Try the Smart Dart Counter App FREE!Ready for an upgrade? Click above!
Why is Flight Ribbing Explained as Important to Aircraft Design?
Aircraft wings aren’t just smooth, curved surfaces. Beneath the skin, a complex framework works tirelessly to maintain the wing’s shape and withstand the immense forces of flight. Flight ribbing plays a vital role in this framework, acting as the backbone that gives the wing its strength and aerodynamic efficiency. Without proper ribbing, a wing would deform under load, leading to reduced lift, increased drag, and potentially catastrophic failure. Understanding the importance of flight ribbing is crucial for comprehending aircraft design and safety.
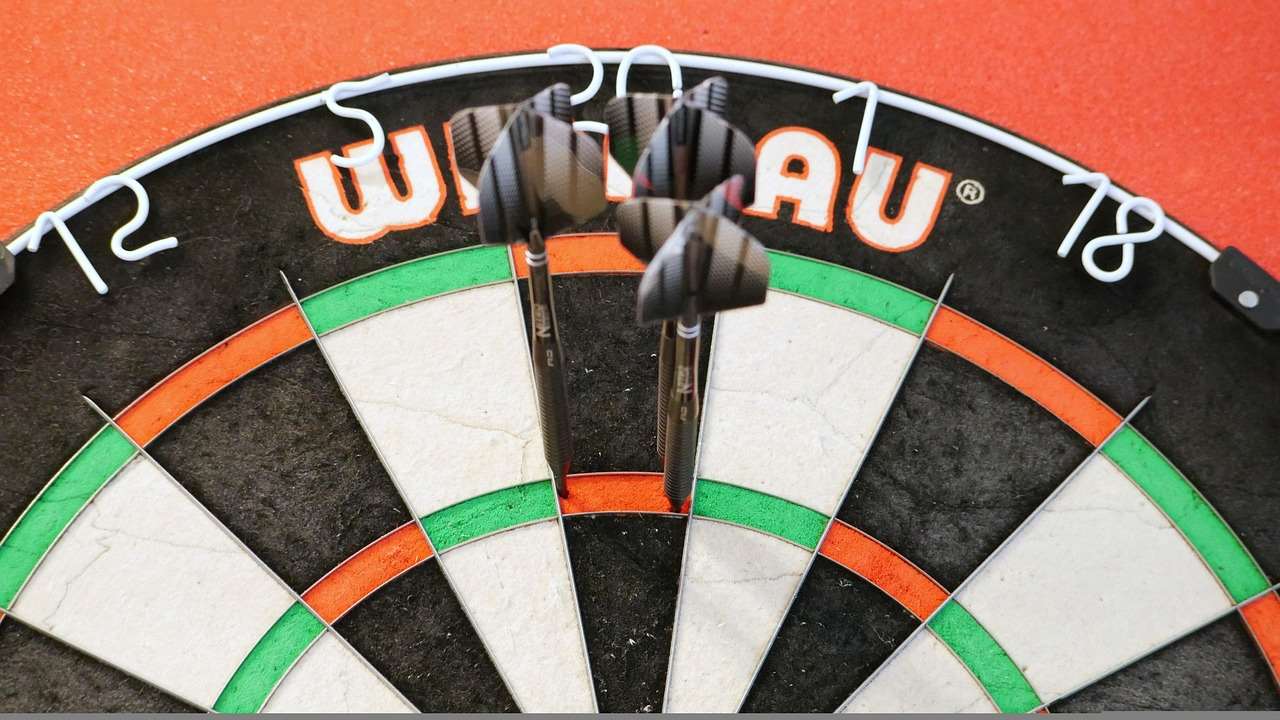
Ribs are essential components within a wing’s internal structure, working in concert with other elements like the spar (the main longitudinal beam) and the skin (the outer covering). They perform several key functions, including:
- Maintaining Airfoil Shape: Ribs are precisely shaped to define the wing’s desired airfoil profile. This profile is critical for generating lift efficiently.
- Distributing Aerodynamic Loads: When air flows over the wing, it creates pressure that needs to be distributed evenly. Ribs help transfer these loads to the spar and other structural members.
- Preventing Skin Buckling: The skin of the wing is relatively thin and can buckle under compression. Ribs provide support to the skin, preventing it from deforming.
- Providing Attachment Points: Ribs often serve as attachment points for control surfaces like ailerons and flaps, as well as for fuel tanks and other internal components.
Different types of ribs are used in aircraft construction, each with its own advantages and disadvantages.
Types of Flight Ribbing
Several types of flight ribbing exist, each suited for particular applications and manufacturing methods. Here’s a look at some of the most common:
Formed Ribs
Formed ribs are typically made from sheet metal that is bent or stamped into the desired shape. They are relatively lightweight and easy to manufacture, making them a popular choice for many aircraft. The thickness of the sheet metal and the design of the rib determine its strength and stiffness. These ribs are often found in the wings of smaller aircraft and control surfaces.
Truss Ribs
Truss ribs consist of a network of struts and braces that form a lightweight yet strong structure. They are particularly effective at distributing loads and resisting deformation. Truss ribs are often used in larger aircraft where high strength and stiffness are required. While offering excellent strength-to-weight ratios, they can be more complex and time-consuming to manufacture compared to formed ribs.
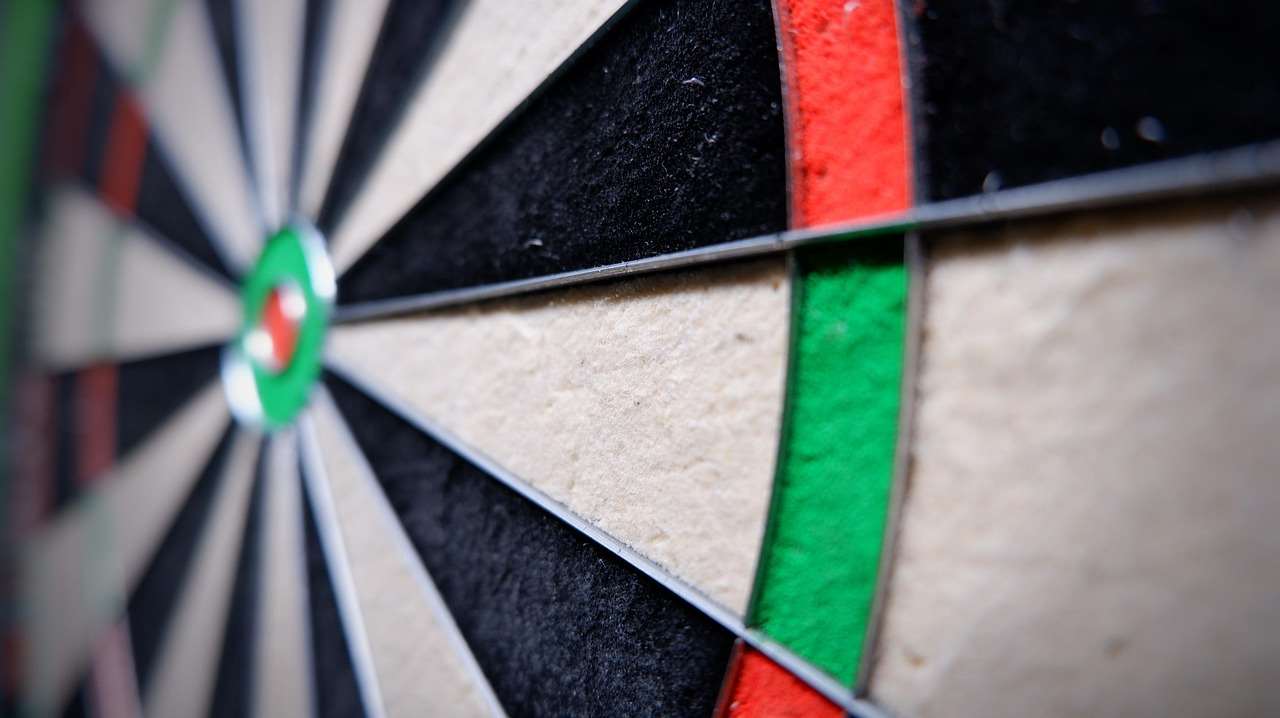
Solid Ribs
Solid ribs, as the name suggests, are made from a single piece of material, often wood or composite. They offer excellent strength and stiffness but are heavier than formed or truss ribs. Solid ribs are typically used in areas where high loads are concentrated, such as at the wing root. Wood ribs are common in older aircraft designs, while composite ribs are used in modern, high-performance aircraft.
Stamped Ribs
Stamped ribs are very similar to formed ribs but are created using a stamping process, which allows for high-volume production and precise shapes. This method is cost-effective for large production runs and ensures consistent rib dimensions. Stamped ribs are commonly found in mass-produced aircraft where uniformity and efficiency are paramount. You can Choose Best Dart Equipment based on factors like material, shape, and intended use.
Materials Used in Flight Ribbing Explained
The materials used for flight ribbing depend on factors like the aircraft’s design, performance requirements, and manufacturing processes. Here are some common materials:
Aluminum
Aluminum alloys are widely used for flight ribbing due to their excellent strength-to-weight ratio, corrosion resistance, and ease of manufacturing. Aluminum ribs can be formed, stamped, or machined to precise dimensions. Different aluminum alloys offer varying degrees of strength and stiffness, allowing designers to tailor the ribbing to specific load requirements. Aluminum is also relatively easy to repair, which is an important consideration for aircraft maintenance.
Wood
Wood, particularly spruce, was a common material for flight ribbing in older aircraft. Wood ribs are lightweight and offer good strength, but they are susceptible to moisture damage and require careful construction and maintenance. While less common in modern aircraft, wood ribs are still used in some vintage aircraft restorations and experimental aircraft projects.

Composites
Composite materials, such as carbon fiber and fiberglass, are increasingly used for flight ribbing in modern aircraft. Composites offer exceptional strength-to-weight ratios and can be molded into complex shapes. They are also resistant to corrosion and fatigue, making them ideal for high-performance aircraft. Composite ribs require specialized manufacturing techniques, but they offer significant advantages in terms of performance and durability. Understanding What Makes Darts Premium Quality can be analogously helpful, as it also involves understanding material properties and construction techniques.
Construction Methods for Flight Ribbing Explained
The construction methods used for flight ribbing vary depending on the type of rib and the materials involved. Here are some common techniques:
Forming and Stamping
Forming and stamping are used to create sheet metal ribs. The sheet metal is bent or stamped into the desired shape using specialized machinery. These processes are cost-effective for high-volume production and ensure consistent rib dimensions. Forming and stamping can create complex rib shapes with features like lightening holes (to reduce weight) and flanges (to increase stiffness).
Welding and Riveting
Welding and riveting are used to assemble truss ribs. Struts and braces are joined together using welding or rivets to create a strong and lightweight structure. Welding provides a strong and permanent joint, while riveting is a simpler and more flexible method. The choice between welding and riveting depends on factors like the materials being joined, the load requirements, and the ease of repair.
Molding and Laminating
Molding and laminating are used to create composite ribs. Layers of composite material are laid up in a mold and then cured under heat and pressure. This process allows for the creation of complex shapes with precise dimensions and excellent strength. Molding and laminating require specialized equipment and skilled technicians, but they offer significant advantages in terms of performance and durability. The quality of the laminate is critical, and this concept connects to the Quality Comparison Budget Premium Darts, where material and construction quality also have a substantial impact.
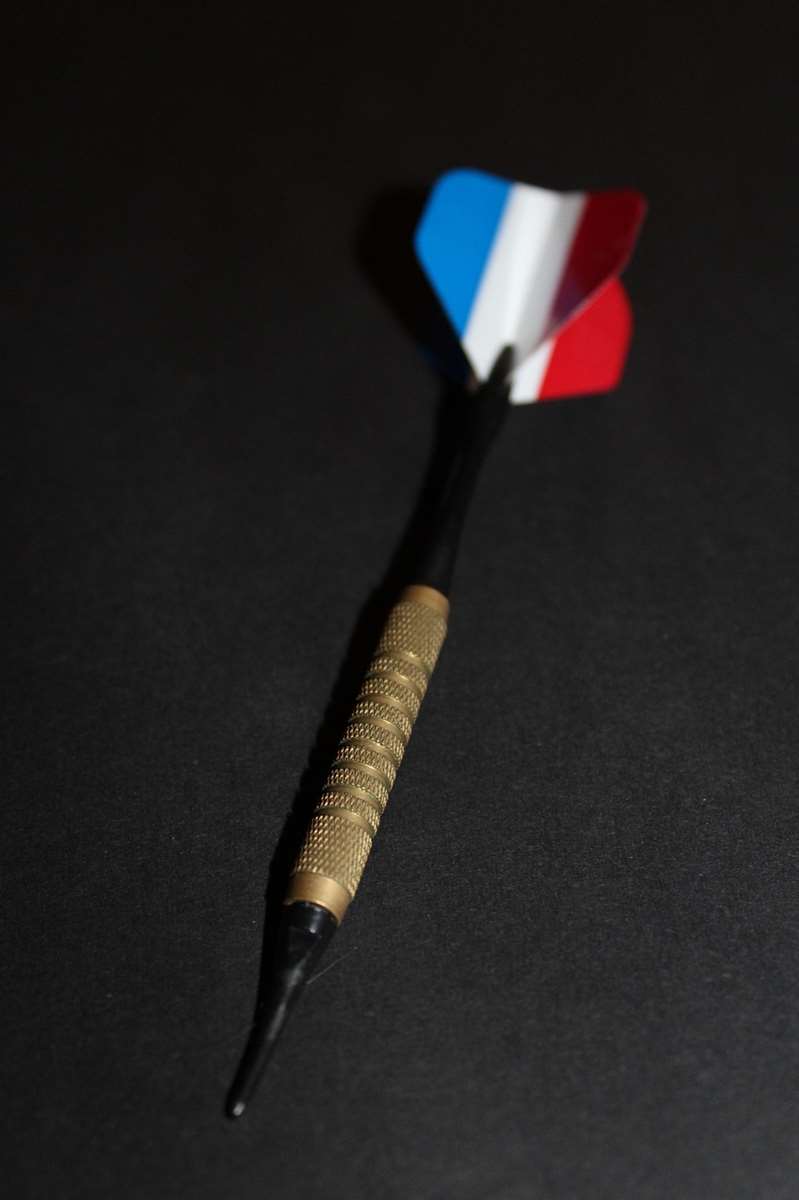
Inspection and Maintenance of Flight Ribbing Explained
Regular inspection and maintenance of flight ribbing are essential for ensuring aircraft safety. Here are some key considerations:
Visual Inspection
Visual inspection is the first line of defense against rib damage. Look for signs of cracks, corrosion, dents, and other damage. Pay close attention to areas around attachment points and stress concentrations. A thorough visual inspection can often reveal potential problems before they become serious.
Non-Destructive Testing
Non-destructive testing (NDT) techniques, such as ultrasonic testing and radiography, can be used to detect hidden cracks and other internal defects. NDT is particularly useful for inspecting composite ribs, where visual inspection may not be sufficient. NDT requires specialized equipment and trained technicians but can provide valuable information about the structural integrity of the ribbing. We can also explore the aspect of Budget vs Premium Darts Compared regarding their maintainability and longevity.
Repair Procedures
Repair procedures for flight ribbing vary depending on the type of rib and the extent of the damage. Minor damage may be repaired by patching or reinforcing the rib. More severe damage may require replacing the entire rib. All repairs must be performed in accordance with approved maintenance manuals and by qualified personnel. Proper repair procedures are crucial for maintaining the structural integrity of the wing and ensuring flight safety.
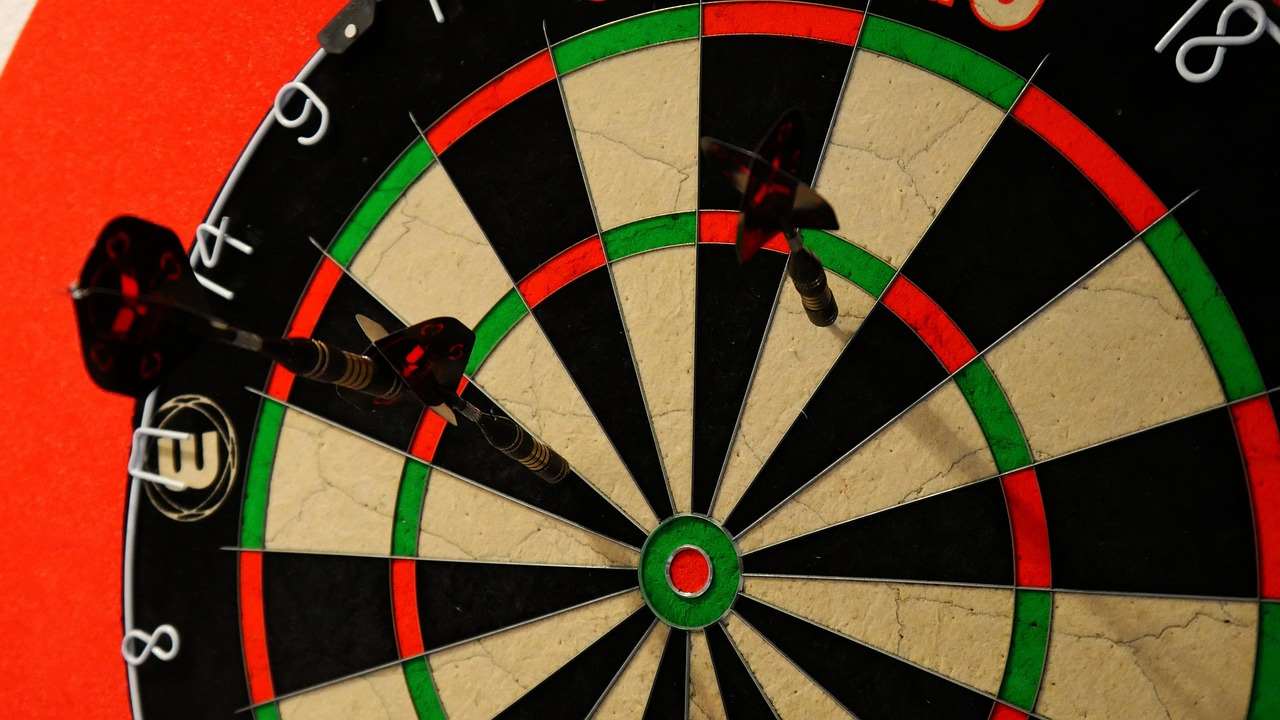
The Future of Flight Ribbing Explained
The future of flight ribbing is likely to see increased use of composite materials and advanced manufacturing techniques. 3D printing, for example, offers the potential to create complex rib shapes with optimized designs. Smart ribs, equipped with sensors to monitor stress and strain, could provide real-time feedback on the wing’s structural health. These innovations promise to further improve the performance, safety, and efficiency of aircraft.
Conclusion
Flight ribbing explained is a crucial aspect of aircraft design, contributing to the wing’s structural integrity, aerodynamic efficiency, and overall safety. From formed ribs to truss ribs, and from aluminum alloys to composite materials, the world of flight ribbing is diverse and constantly evolving. Regular inspection and maintenance are essential for ensuring the continued airworthiness of aircraft. As technology advances, we can expect to see even more innovative approaches to flight ribbing that will further enhance the performance and safety of future aircraft. If you are interested in learning more about aircraft structures, consider researching further into related topics or consulting with an aerospace engineer.
Hi, I’m Dieter, and I created Dartcounter (Dartcounterapp.com). My motivation wasn’t being a darts expert – quite the opposite! When I first started playing, I loved the game but found keeping accurate scores and tracking stats difficult and distracting.
I figured I couldn’t be the only one struggling with this. So, I decided to build a solution: an easy-to-use application that everyone, no matter their experience level, could use to manage scoring effortlessly.
My goal for Dartcounter was simple: let the app handle the numbers – the scoring, the averages, the stats, even checkout suggestions – so players could focus purely on their throw and enjoying the game. It began as a way to solve my own beginner’s problem, and I’m thrilled it has grown into a helpful tool for the wider darts community.